Custom Chrome on Quartz Glass Target
High Precision • Custom • MOQ 1pcs
- Good Thermal Expansion Coeff (CTE) performance
- Standard feature size accuracy +/-1μm
- Best feature size accuracy +/-1μm
- Standard feature position accuracy +/-1μm
- Maximum size 1200x850mm
- Smallest line width/ minimum feature size down to 0.5um;
- Graticules, scales, reticles, pin holes, apertures, calibration targets, resolution targets, test targets
Precision Standards
Accuracy Specification | ||||
---|---|---|---|---|
Feature Size Accuracy | Dot Diameter | ±0.001mm / ±0.0001mm | Circularity | 0.001mm |
Square/Checker Size | Line Straightness (mm) | 0.001mm | ||
Line Width | ||||
Feature Spacing Accuracy
(Any 2 Neighbor Features) |
Dot Spacing | ±0.001mm / ±0.0001mm |
Distance Accuracy
(from Chrome Pattern to Target Edge) |
±0.05mm, ±0.1mm |
Chessgrid Corner to Corner Spacing | ||||
Line Spacing | ||||
Feature Position Accuracy
(in Entire Pattern Area against ideal position):ChessGrid Corner Position, Circle Position, etc |
Dimension <= 300mm | ±0.001mm |
Accuracy Certificate
(3rd-Party/ CalibVision) |
Available on Request |
Dimension > 300mm | ±0.003~0.005mm |
Minimum Feature Size | ||||
---|---|---|---|---|
Smallest Feature Size | Dot Diameter | Down to 0.5μm | ||
Dot Spacing | ||||
Line Width | ||||
Checker Size |
Properties | Data & Specification | |||
---|---|---|---|---|
Size Range:
Length/Width(mm) |
1×1mm to 1200×850mm | Thickness Options: | 1.5 / 2.3 / 3.0 / 10.0mm | |
Dimension Tolerance (mm) : | ±0.05mm, ±0.1mm | Thickness Tolerance (mm) | ±0.1mm | |
Edges | Beveled | Angle of the edges | ±1° | |
Surface Flatness (um) | Dimension <130mm: | ~5um | Surface Roughness | <0.025um |
Dimension 130-220mm: | ~10um; | |||
Dimension 220-450mm: | ~20um; | |||
Dimension 220-450mm: | ~20um; |
Properties | Value | Properties | Value |
---|---|---|---|
Reflectance (420~700nm) |
Rave<3.643%@420~700nm
(Reflectance can be optimized to Rave<0.3% by applying AR coating on glass surface if needed) |
Transmission |
Tmax <93.709%@420~700nm (Transmittance can be optimized to Tmax<99.2% by applying AR coating on glass surface if needed) |
Refractive Index | 1.4701@400nm; | Surface Quality | Scratch:Dig<=40:20 |
1.4585@587nm; | |||
1.4553@700nm; | |||
Coefficient of Thermal Expansion (CTE) (15 to 200 ℃) | <5.0*10⁻⁷ | Manufacturing Temperature(°C) | 23°C |
Compressive Strength | 1100Mpa | Bending Strength / Flexural Strength | 67Mpa |
Tensile Strength | 48Mpa | Poisson's Ratio | 0.14-0.17 |
Young Modulus | 72000Mpa | Modulus of rigidity | 31000Mpa |
Moh's hardness | 7 | Operating Temperature | -40°C to +1100°C |
Dielectric Constant | 3.7-3.9MHz | Coefficient of Thermal Conductivity(°C) | 1.47/m°C |
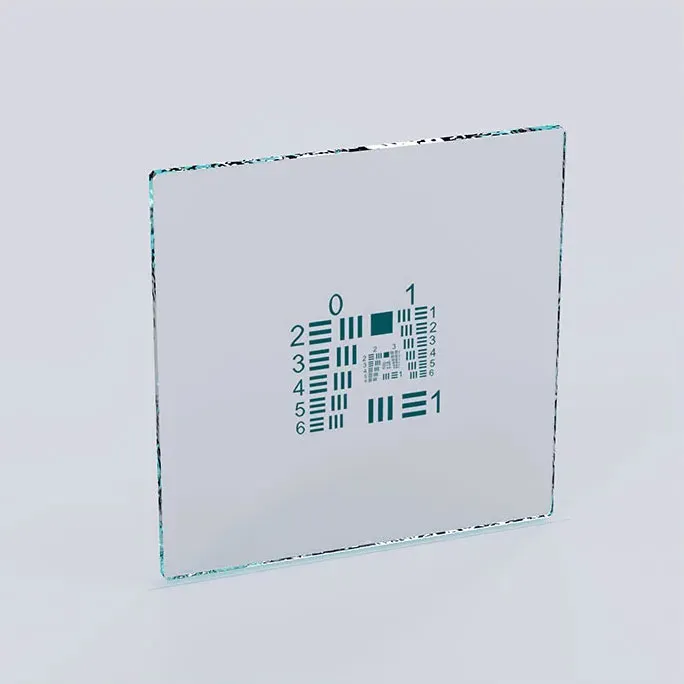
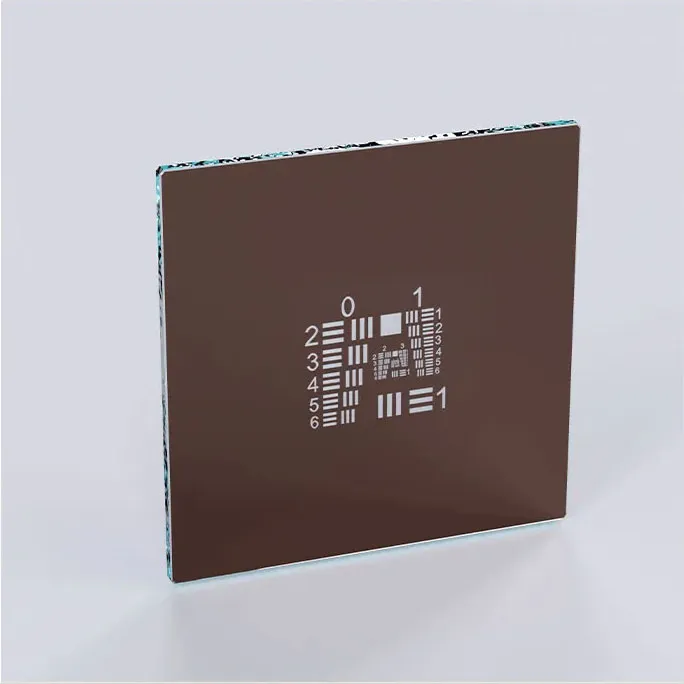
Why Choose Chrome on Glass Substrate?
The superior substrate choice for the most demanding calibration applications
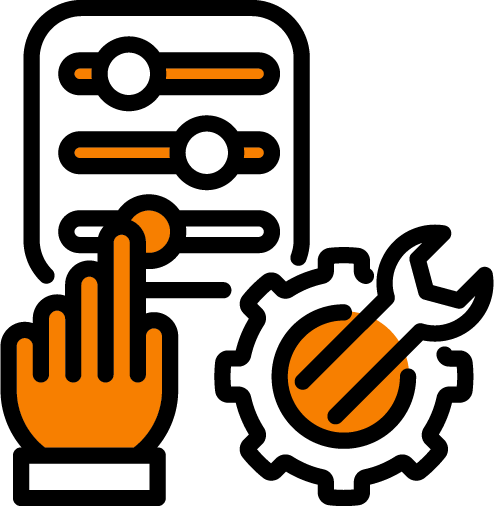
Ultimate Feature Resolution
Minimum feature size down to 0.5μm with razor-sharp edges. Lithographic process delivers unmatched pattern definition and contrast.
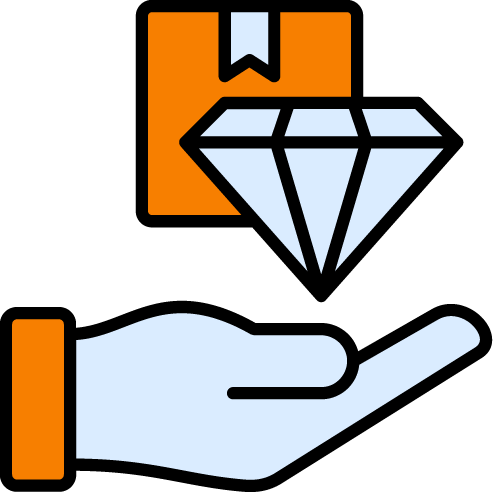
Ultra-Low Thermal Expansion
Coefficient of thermal expansion <5×10⁻⁷/°C - 15× better than standard glass. Maintains precision across temperature variations from -40°C to +1100°C.
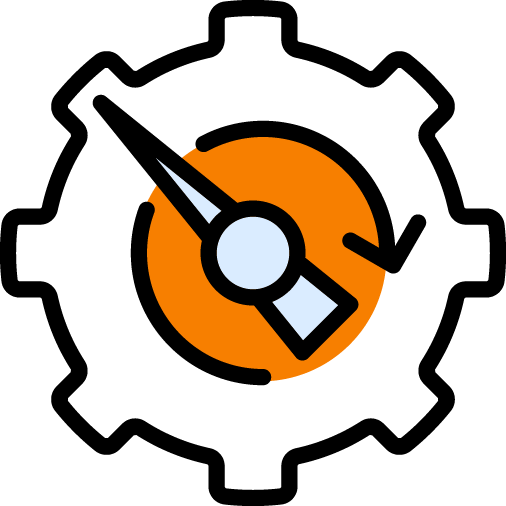
Superior Optical Properties
High transmission (>93%) across visible spectrum with excellent homogeneity. Perfect for backlight and transmission illumination setups.
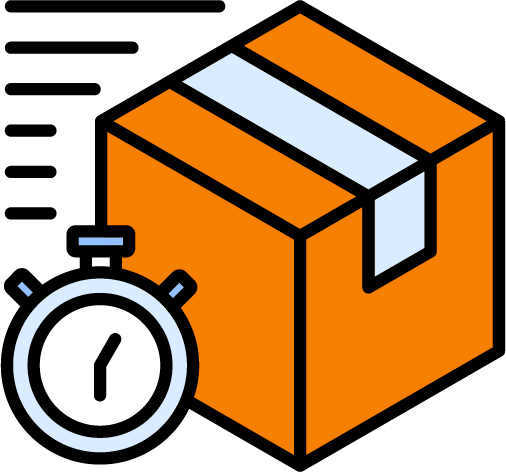
Exceptional Flatness
Surface flatness down to 5μm for targets up to 130mm. Critical for applications requiring consistent optical path length across the entire surface.
Minimum Line/space
Why Substrate Choice Matters for Your Application
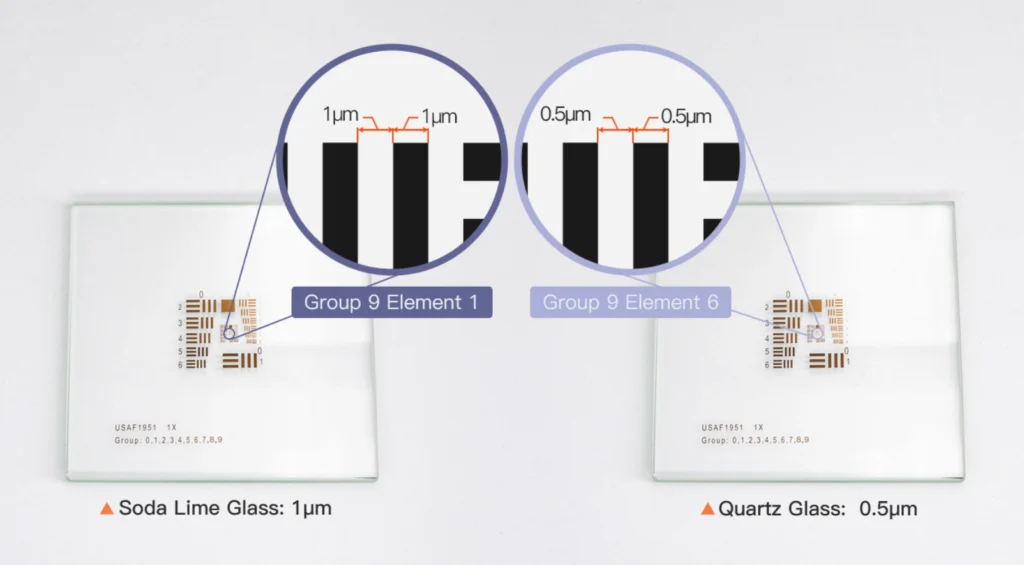
Substrate Properties Comparison
Thermal Expansion Coeff
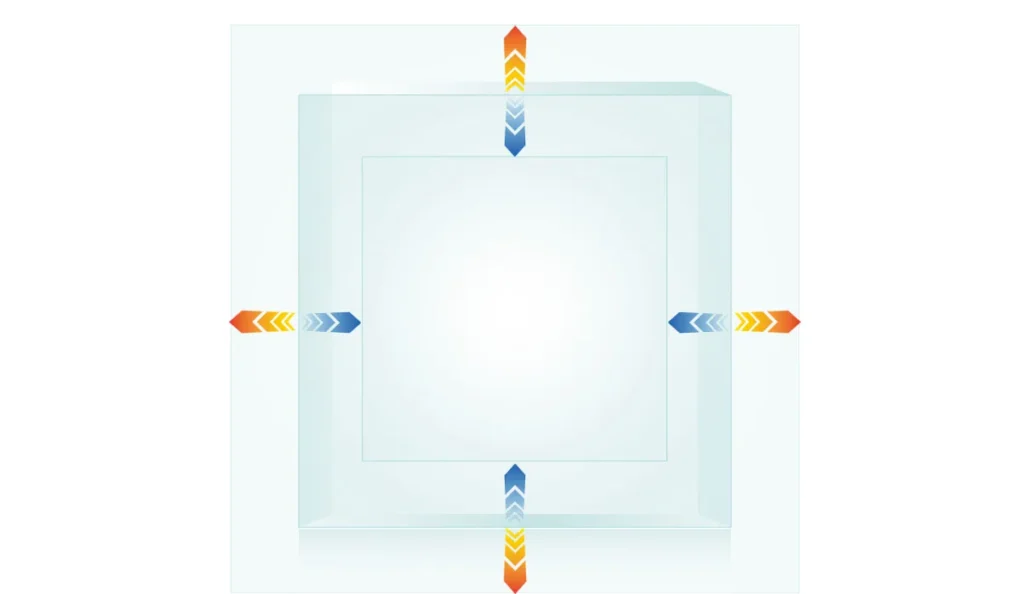
What is Thermal Expansion Coeff in Glass Substrates??
Parameters
Soda Lime Glass (Float Glass)
Quartz Glass (Fused Silica)
Thermal Expansion Coeff (15-200 ℃)
<8.0×10 -7/K
<5.0×10-7 /K
Expansion Ratio (20-200 ℃)
0.00085%
0.00006%
Real-World Expansion Impact of 1 Meter
1m glass changes by 8.5μm per 1°C
1m glass changes by 0.6μm per 1°C
Temperature Stability
Standard stability
14x more stable
Best Applications
General-purpose testing
Precision measurement systems
One of the advantages of quartz glass is Low Thermal Expansion Rate (CTE): <5.0*10⁻⁷, it delivers superior thermal stability (0.55μm/°C vs 8.5μm/°C). Essential for precision measurements, optional for general testing applications.
Unless you need exceptional thermal stability, soda lime glass delivers excellent performance at a fraction of the cost of quartz glass.
Superior Light Transmission
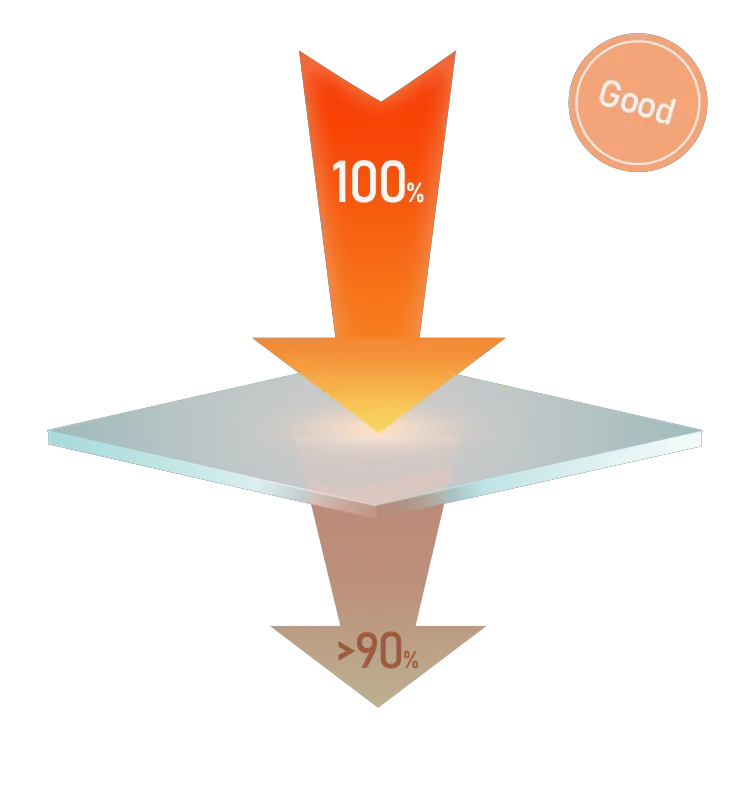
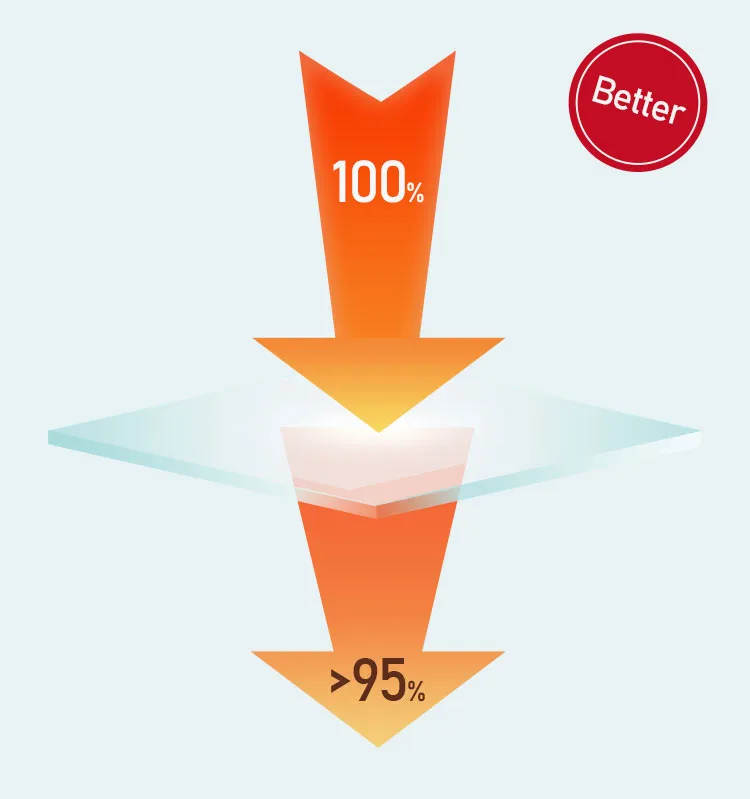
Surface Flatness Comparison
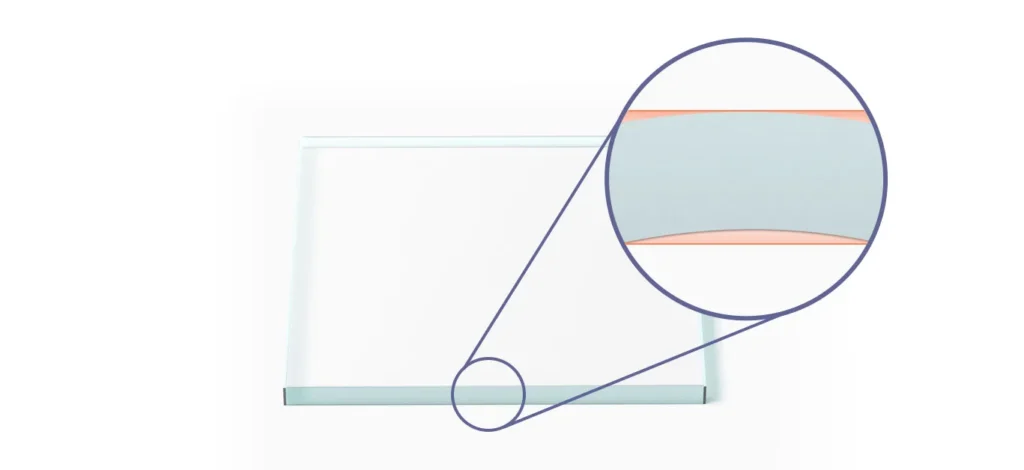
Note: Quartz glass consistently delivers 5-10× better surface flatness across all size ranges, making it ideal for precision optical applications.
What is Surface Flatness?
Glass Type
Soda Lime Glass (Standard Float Glass)
Quartz Glass (Fused Silica)
Small Samples
Surface Deviation
<5μm (for sizes under 100mm)
<1μm (for sizes under 50mm)
Medium Samples
Surface Deviation
<20μm (for sizes under 200mm)
<2μm (for sizes under 100mm)
Large Samples
Surface Deviation
<50μm (for sizes over 200mm)
<5μm (for sizes over 100mm)
Ultra-Smooth Surface
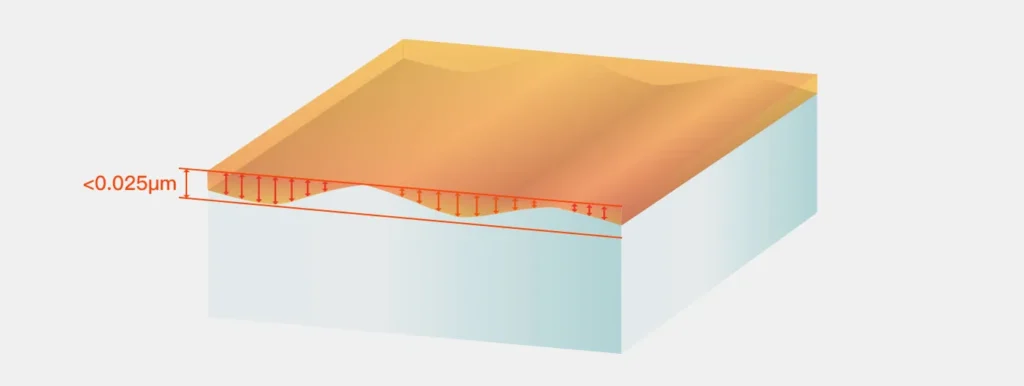
Note: Diagram shows microscopic surface profile with maximum height variations under 25nm
Our precision-polished quartz glass features an exceptionally smooth surface with microscopic variations of less than 0.025μm (25nm) – approximately 2,000 times thinner than a human hair.
- Superior optical performance
- Minimal light scatter
- Optimal coating adhesion
- Exceptional image clarity
Diagram shows microscopic surface profile with maximum height variations under 25nm
Types of Chrome Coating on Glass Test Target
Low Reflectivity Quartz Glass
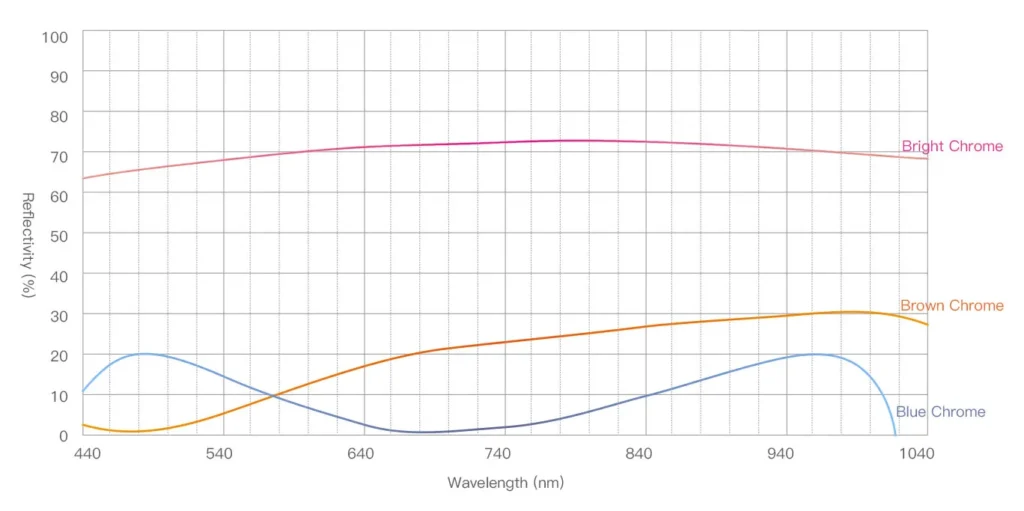
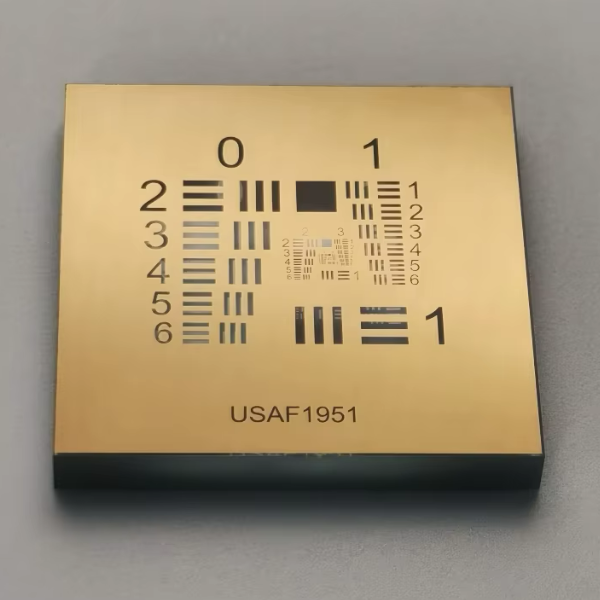
Standard Brown Chrome
- Best for: General-purpose applications
- Reflectivity: <25% for good contrast
- Cost-effective choice when extreme precision isn’t critical
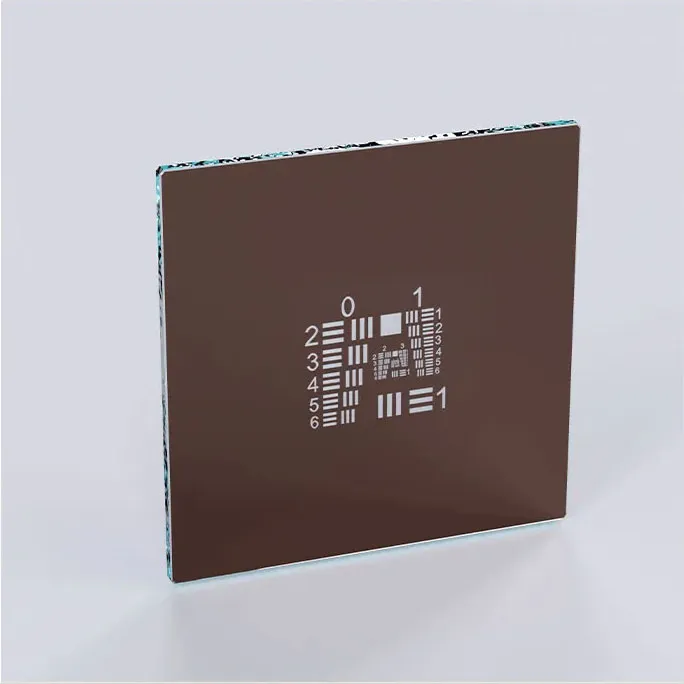
Low-Reflective Blue Chrome
- Best for: High-contrast applications
- Reflectivity: <5% for maximum contrast
- Ideal when you need to eliminate stray light
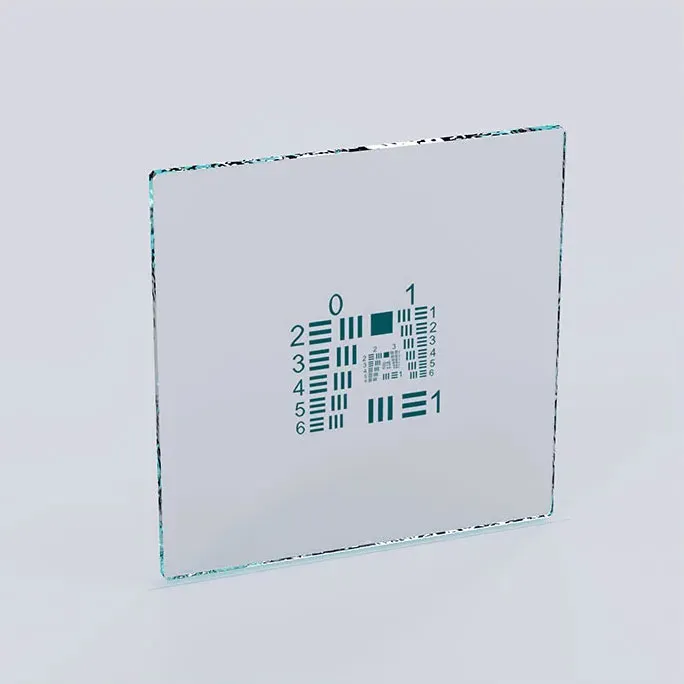
High-Reflective Silver Chrome
- Best for: Reflective measurement systems
- Reflectivity: <65% for bright reference patterns
- For applications requiring reflected light
Standard Type - Dark Brown Chrome
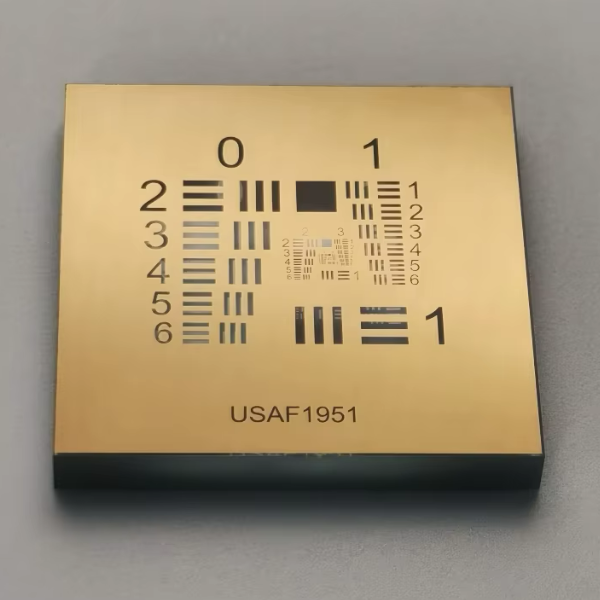
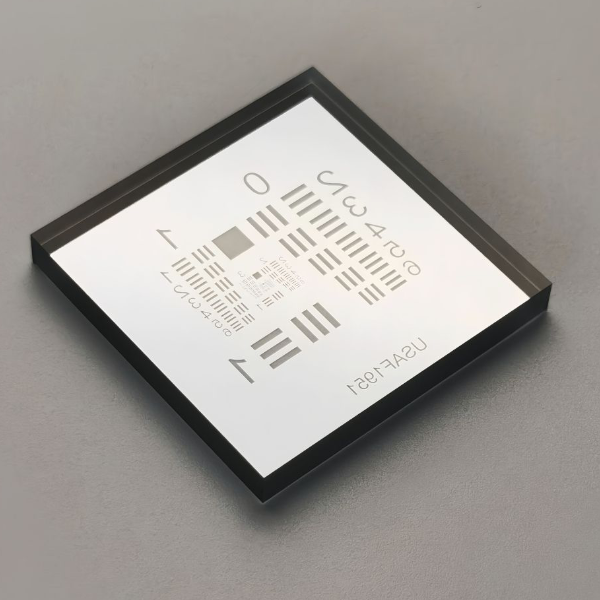
Front Surface/Air Side Brown (Front View)
Glass Side Silver (Back View)
Custom Type - Blue Chrome - Silver
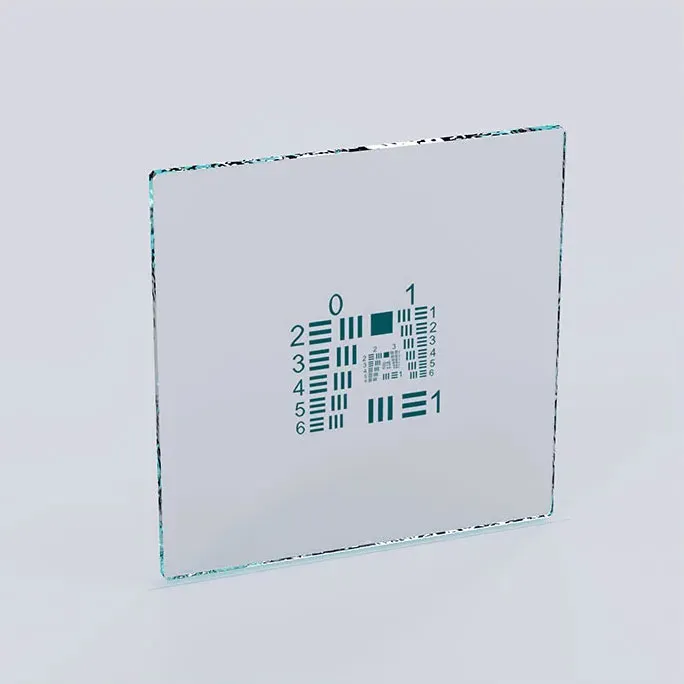
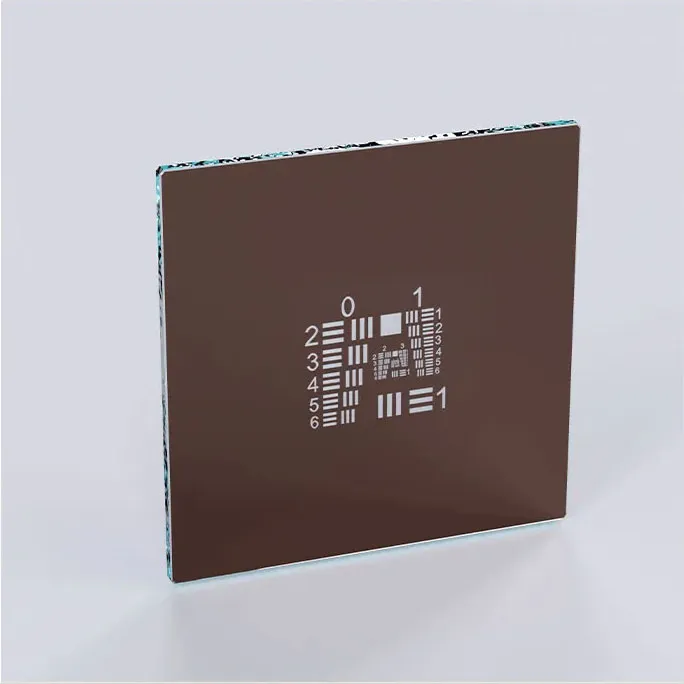
Front Surface/Air Side Blue (Front View)
Glass Side Silver (Back View)
Custom Type - Blue Chrome - Blue
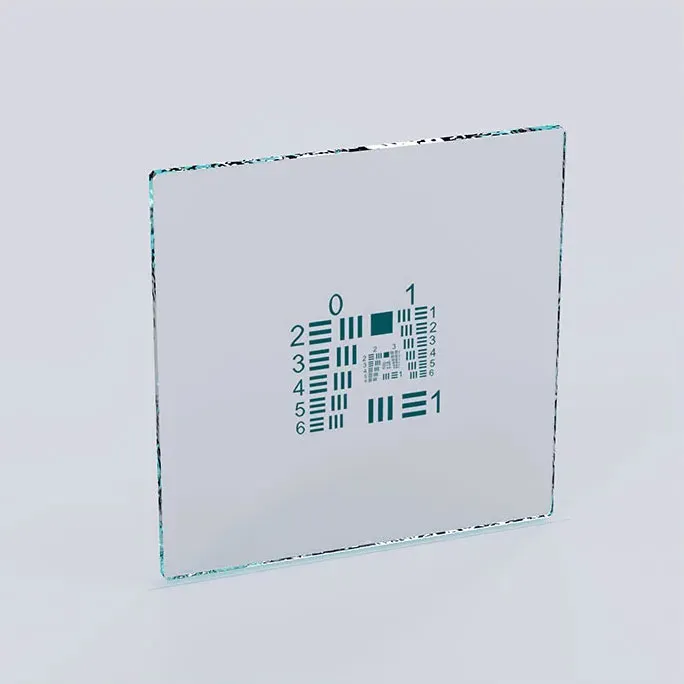
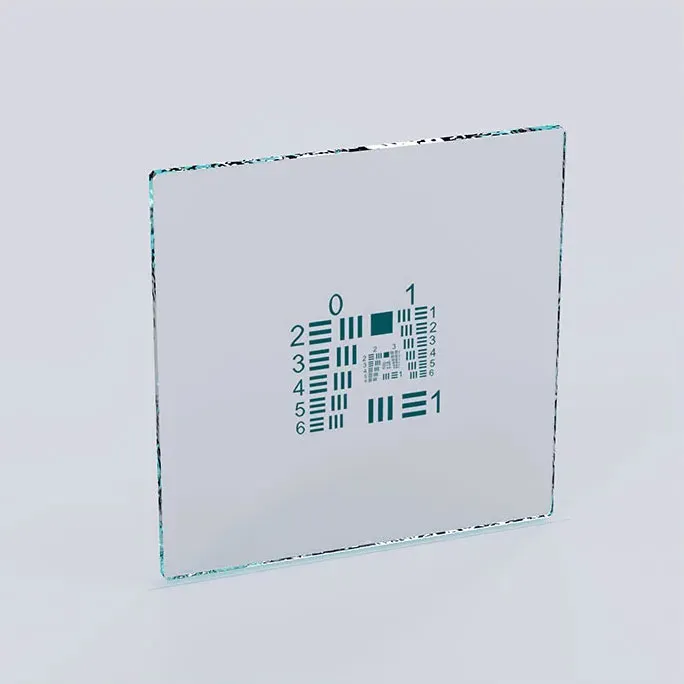
Front Surface/Air Side Blue (Front View)
Glass Side Silver (Back View)
Custom - High-Reflective Chrome (Silver)
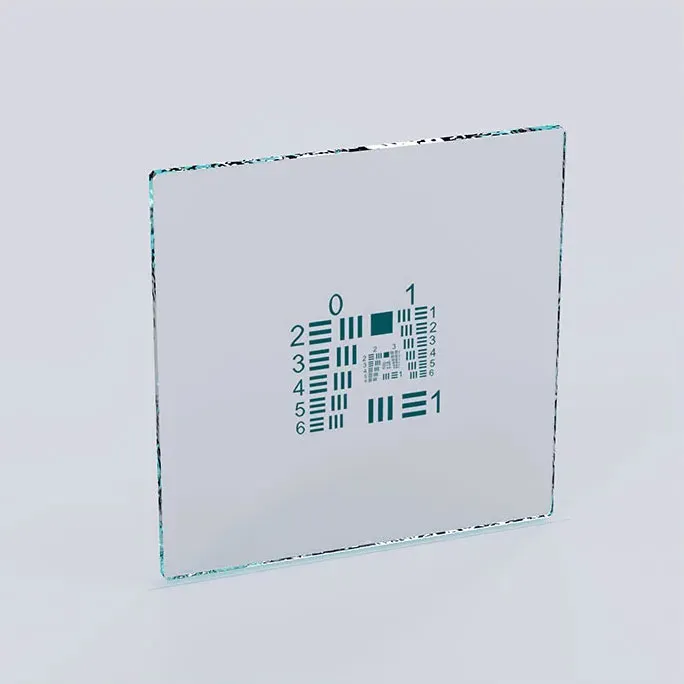
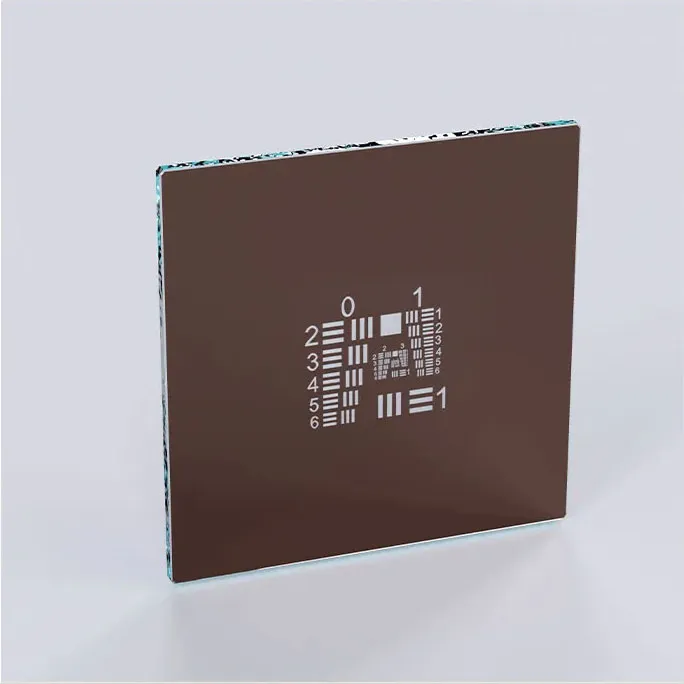
Front Surface/Air Side Silver (Front View)
Glass Side Silver (Back View)
Choose Your Ideal Chrome Coating
Based on the demonstrated reflectivity performance, select the coating that matches your application’s contrast and measurement requirements. Each option delivers consistent, reliable results for different optical testing scenarios.
Contact us to specify your preferred chrome coating option, or request samples to test with your specific setup.
Custom Test Targets Precision Thickness Options
Ultra-thin for compact designs
Standard precision applications
Enhanced durability
Maximum stability
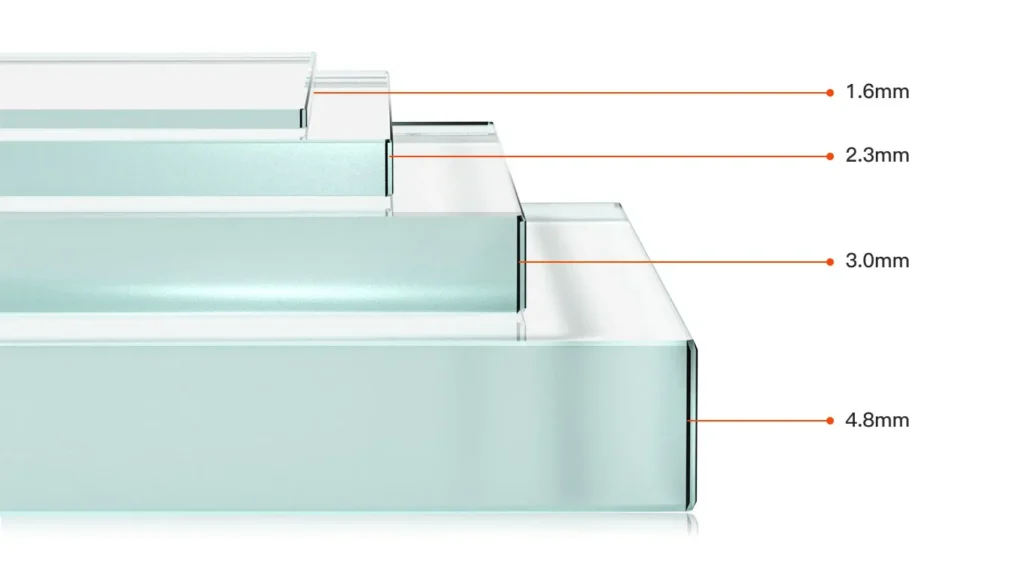
Size & Dimension & Tolerance
Properties | Value | Value | ||
---|---|---|---|---|
Size Range:
Length/Width(mm) |
1×1mm to 1200×850mm | Thickness Options: | 1.5 / 2.3 / 3.0 / 10.0mm | |
Dimension Tolerance (mm) : | ±0.05mm, ±0.1mm | Thickness Tolerance (mm) | ±0.1mm (Consistent optical path length) | |
Edge Finish | Beveled ±1° | Purpose | Prevents edge damage and light scattering | |
Surface Flatness (um) | Dimension <130mm: | ~5μm | Surface Roughness | <0.025μm for optimal optical quality |
Dimension 130-220mm: | ~10μm | |||
Dimension 220-450mm: | ~20μm | |||
Dimension 220-450mm: | ~20μm |
Density Measurement
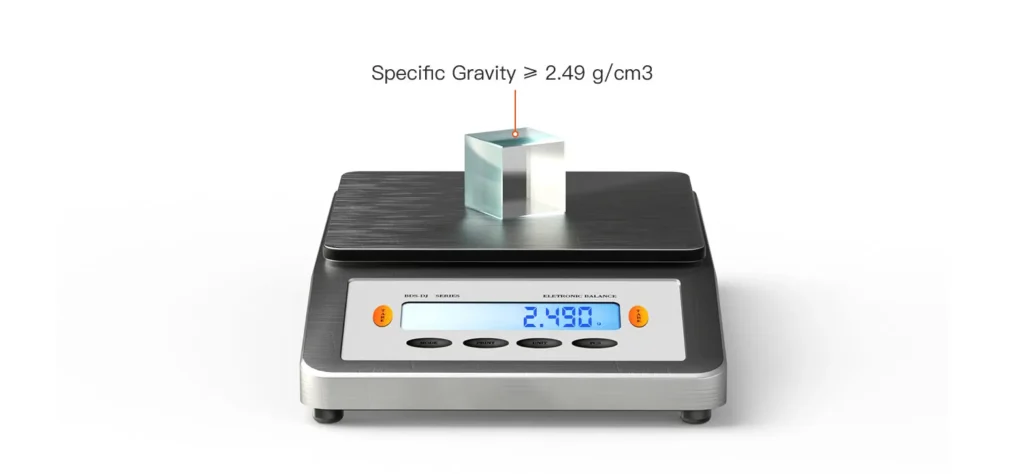
Custom Calibration Targets Dimensional Range
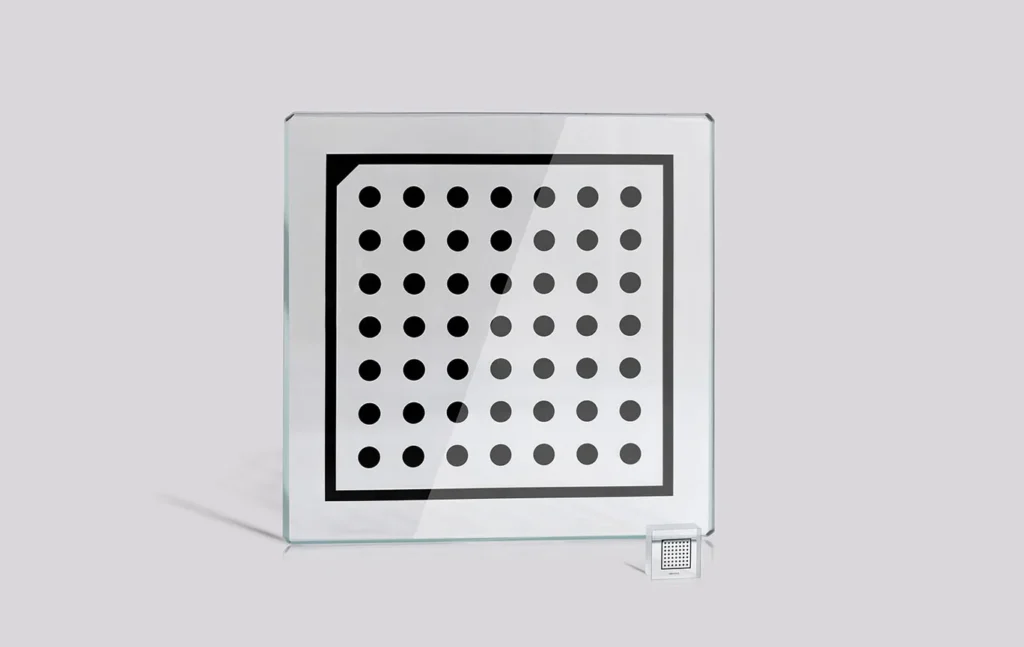
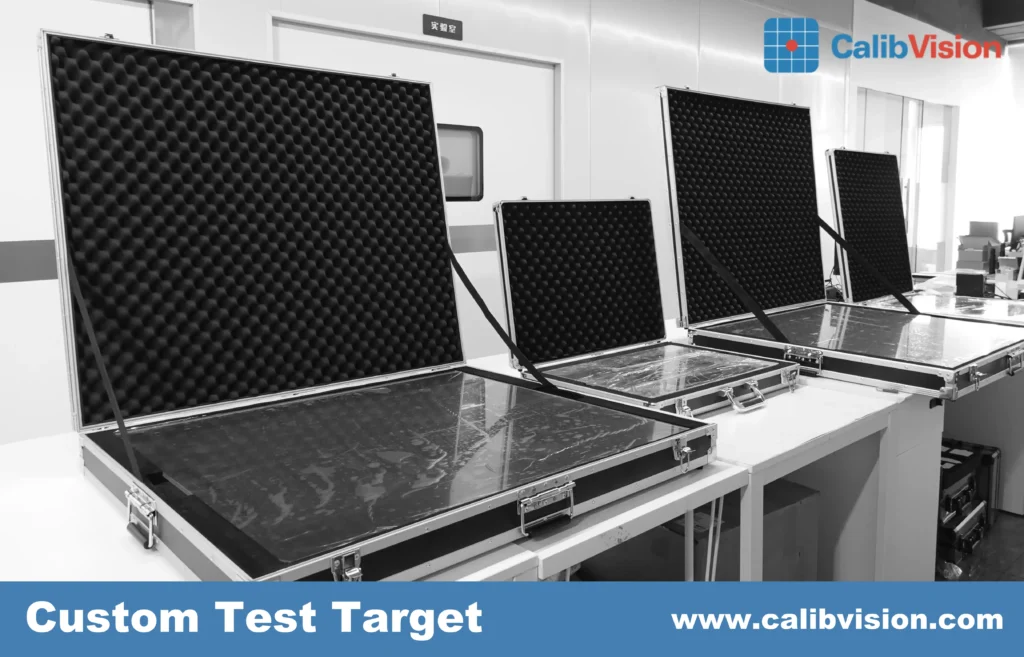
Precision Laser Cutting Custom Shapes Made Easy
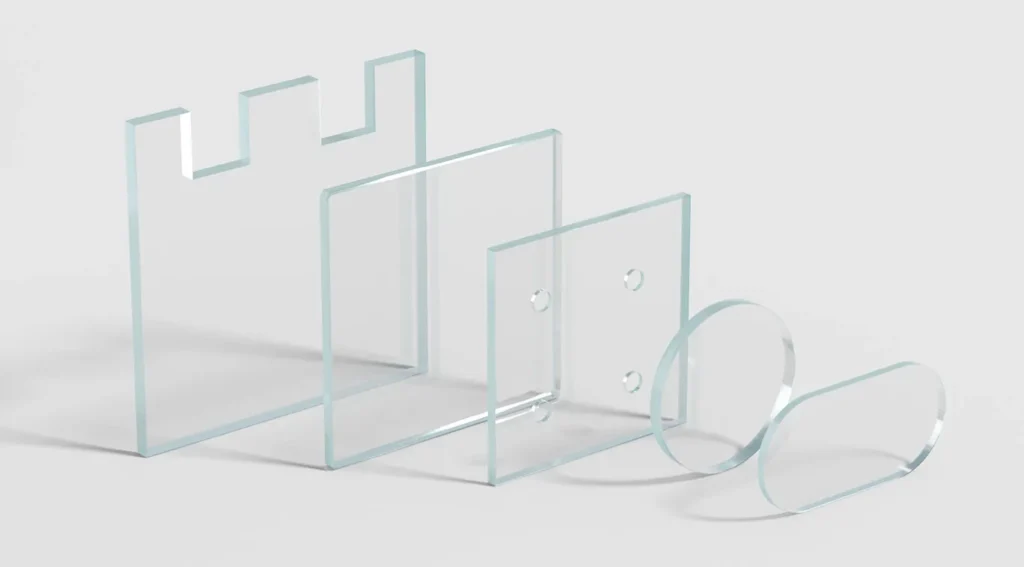
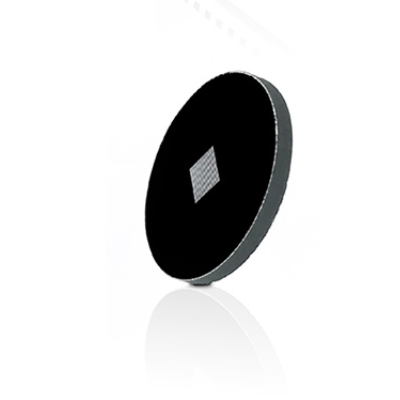
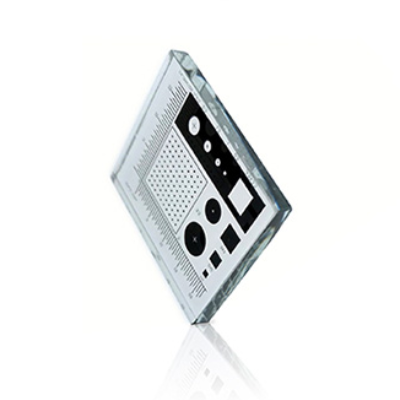
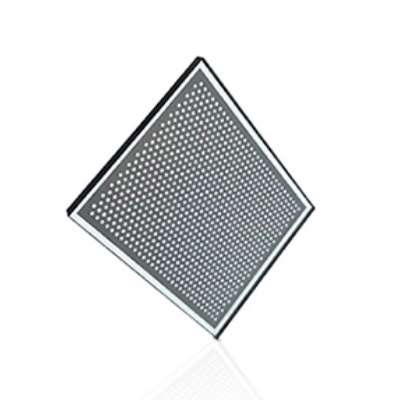
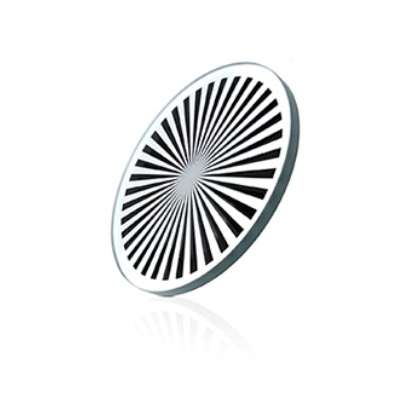

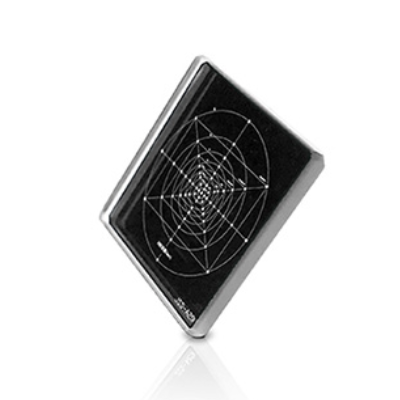
Chrome Test Target Manufacturing
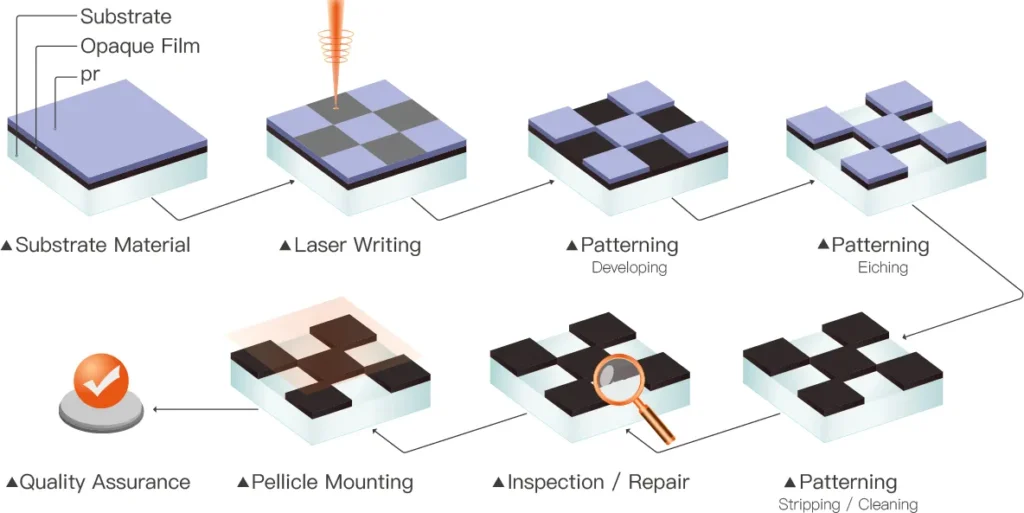
Manufacturing Workflow:
Substrate Material
Step 1: High-quality glass or quartz substrate preparation with optical-grade surface finish and flatness specifications.
Laser Writing
Step 2: Precision laser systems create the photoresist pattern with sub-micrometer accuracy, defining the exact resolution groups and elements.
Developing
Step 3: Chemical developing process reveals the exposed photoresist areas, creating the initial pattern structure ready for etching.
Etching
Step 4: Selective etching removes material to create the final high-contrast resolution patterns with sharp, well-defined edges.
Pellicle Mounting (Optional)
Step 5: Protective pellicle film installation provides contamination protection while maintaining optical access to the target patterns.
Inspection & Repair
Step 6: Comprehensive quality control using advanced optical inspection systems to verify feature accuracy and pattern integrity.
Stripping & Cleaning
Step 7: Final photoresist removal and precision cleaning ensures optimal optical performance and long-term stability.
Quality Assurance
Step 8: Final verification testing confirms all specifications meet USAF 1951 standards with documented traceability and certification.
What Makes Our Test Targets Excellent
Automatic Post-treatment
Spin Coating Equipment
3D Automatic Measuring
IC-Mask Writer Equipment
AOI Inspection Equipment
Optical Density Meter
Precision Backlighting for Glass Calibration Targets
- Large illumination area: 2.1 × 1.4 m
- Superior uniformity: 95%
- Dual-spectrum capability: IR and visible light
- High brightness output
- Ultra-slim profile
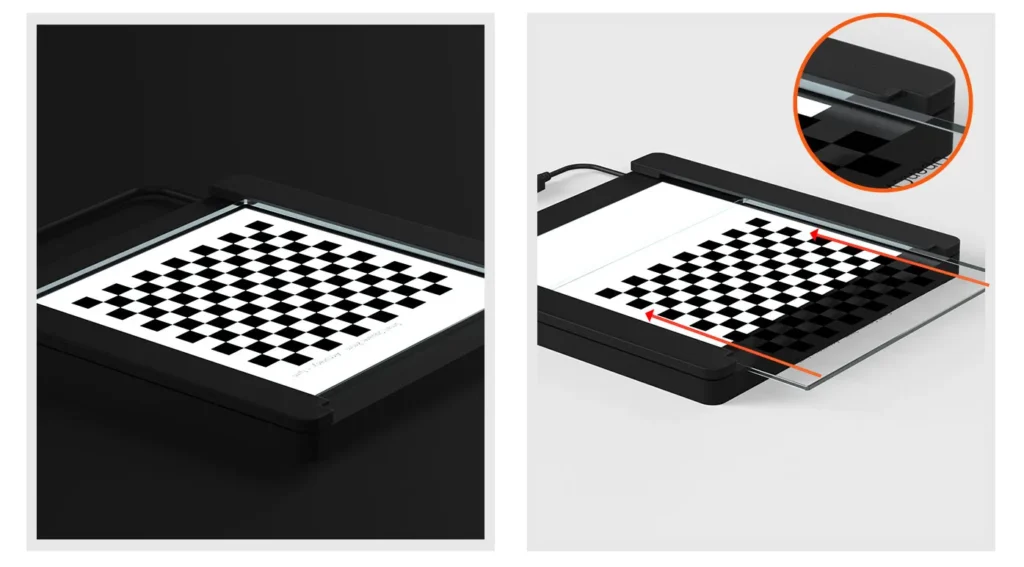
Perfect Applications
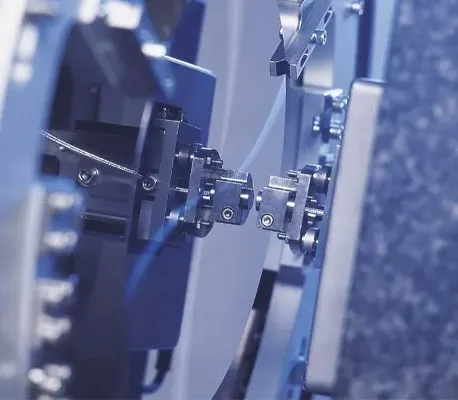
Industrial Measurement
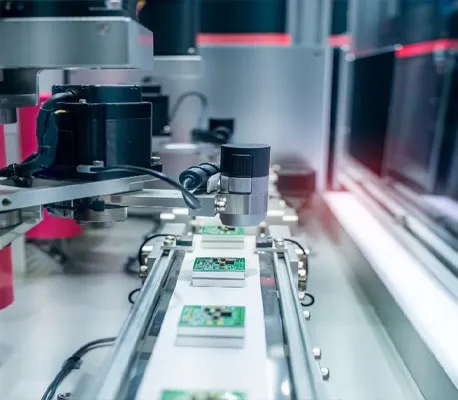
Machine vision
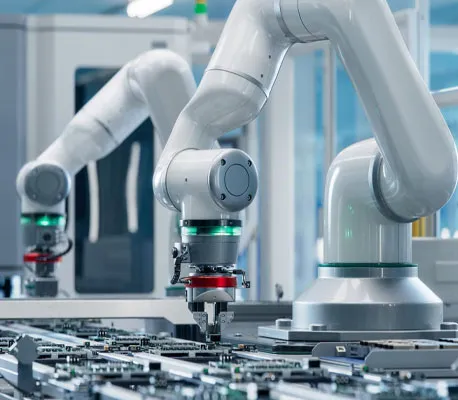
Factory Automation
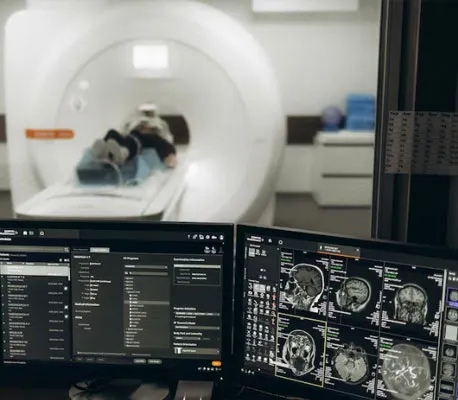
Medical Imaging
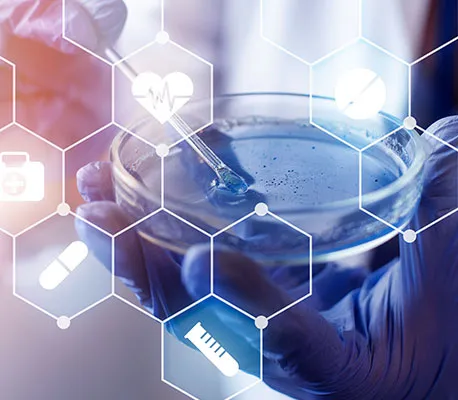
Scientific Research
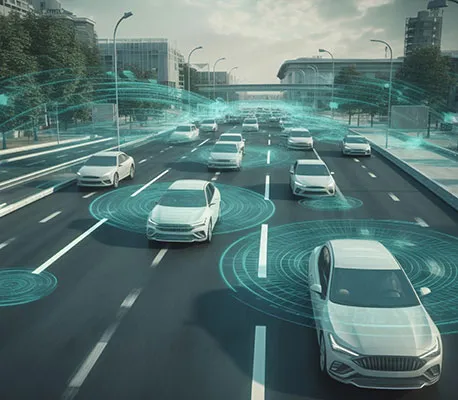
Autonomous Vehicle Vision
Why Custom Chrome Test Targets from us?
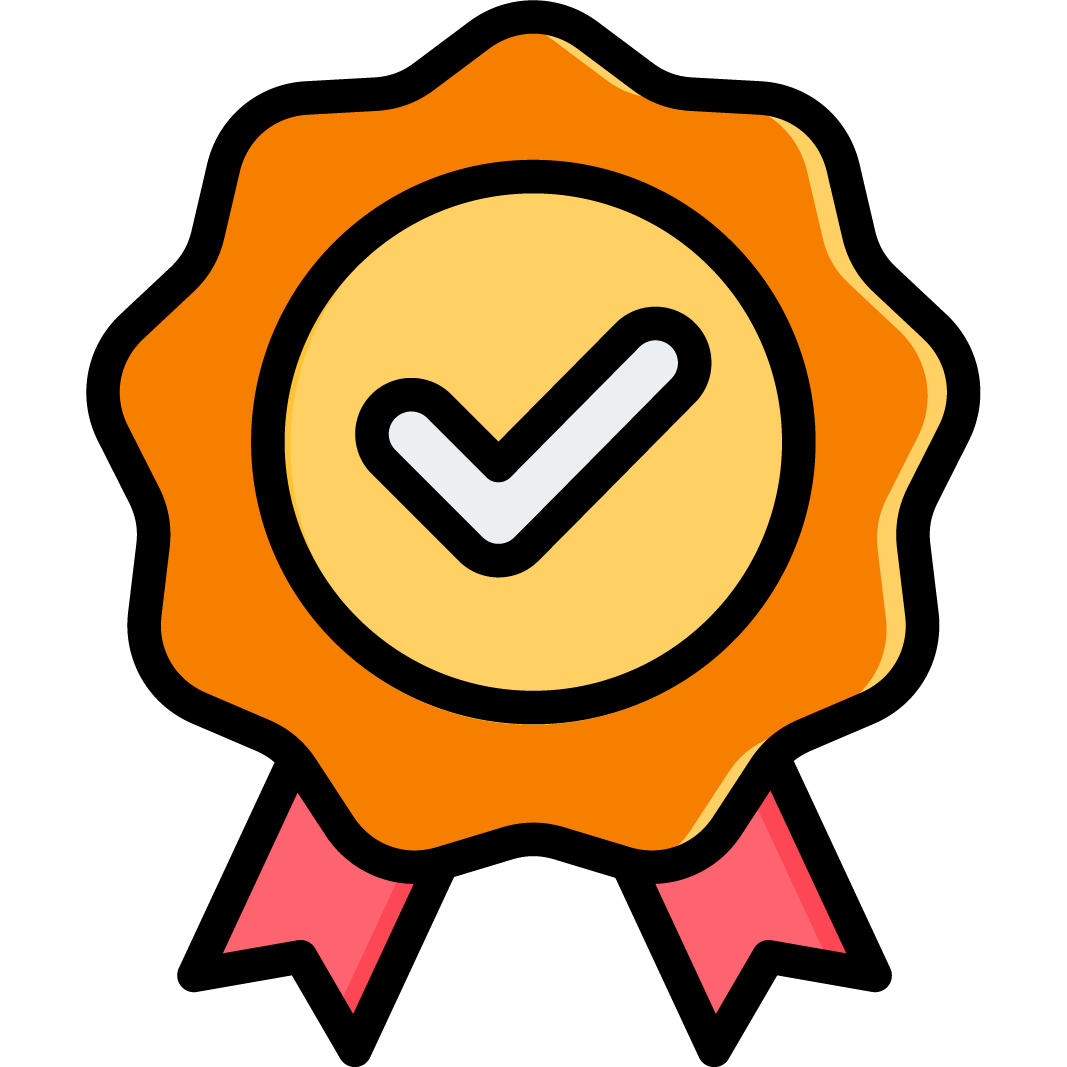
Certified Quality
Independent third-party certification available upon request.
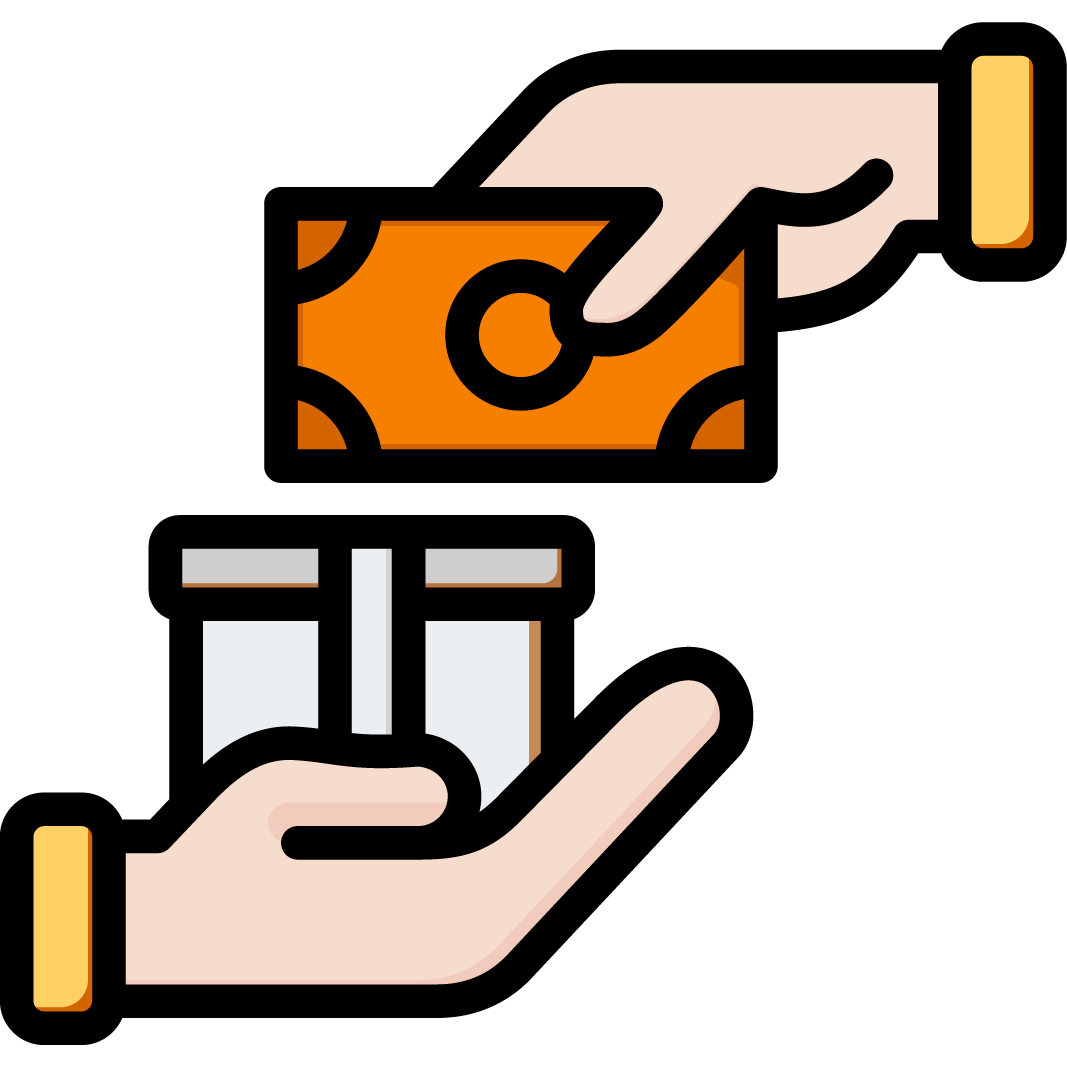
No Minimum Order
Single-piece orders welcome – no quantity requirements.
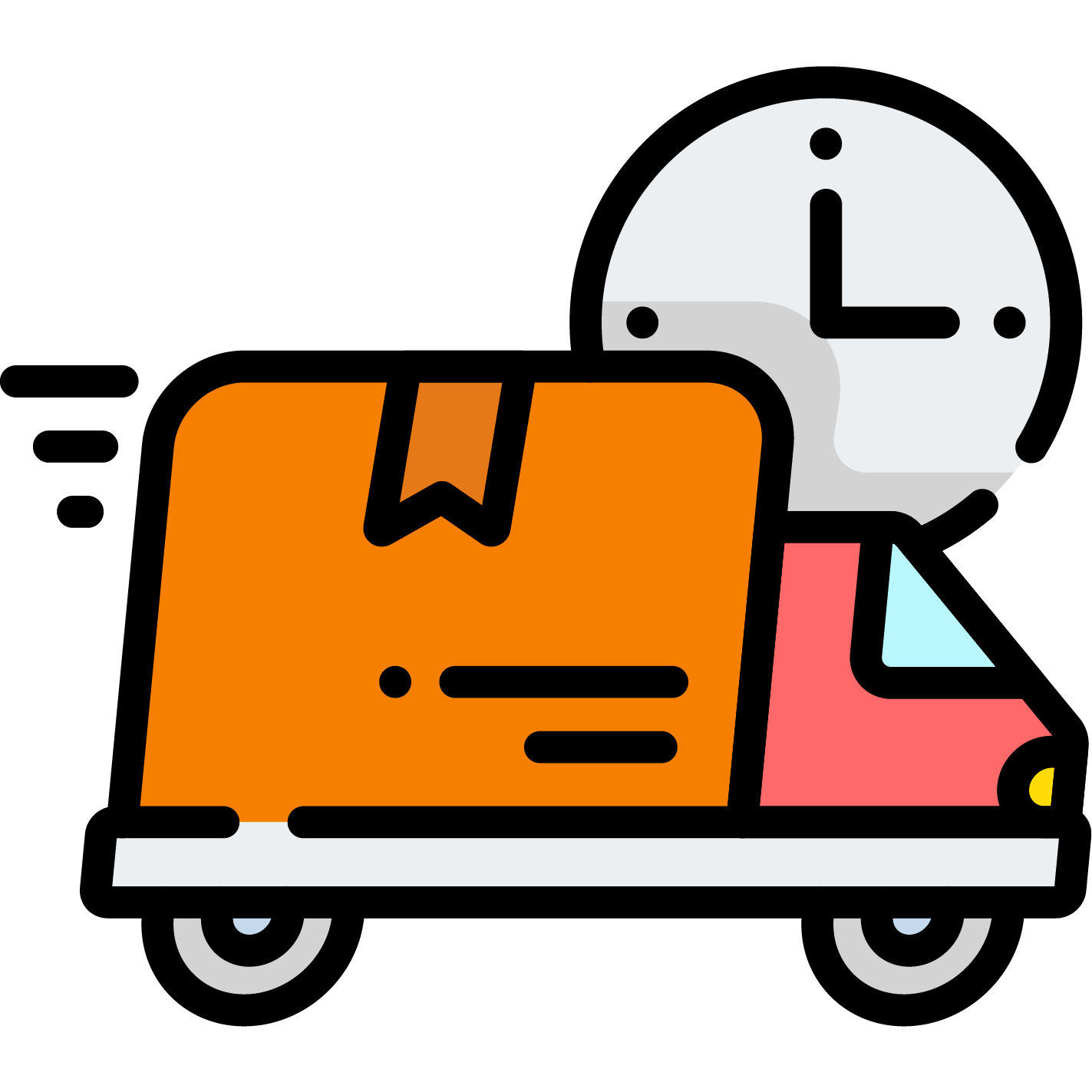
Fast Delivery
Custom production completed in just 5-10 business days.
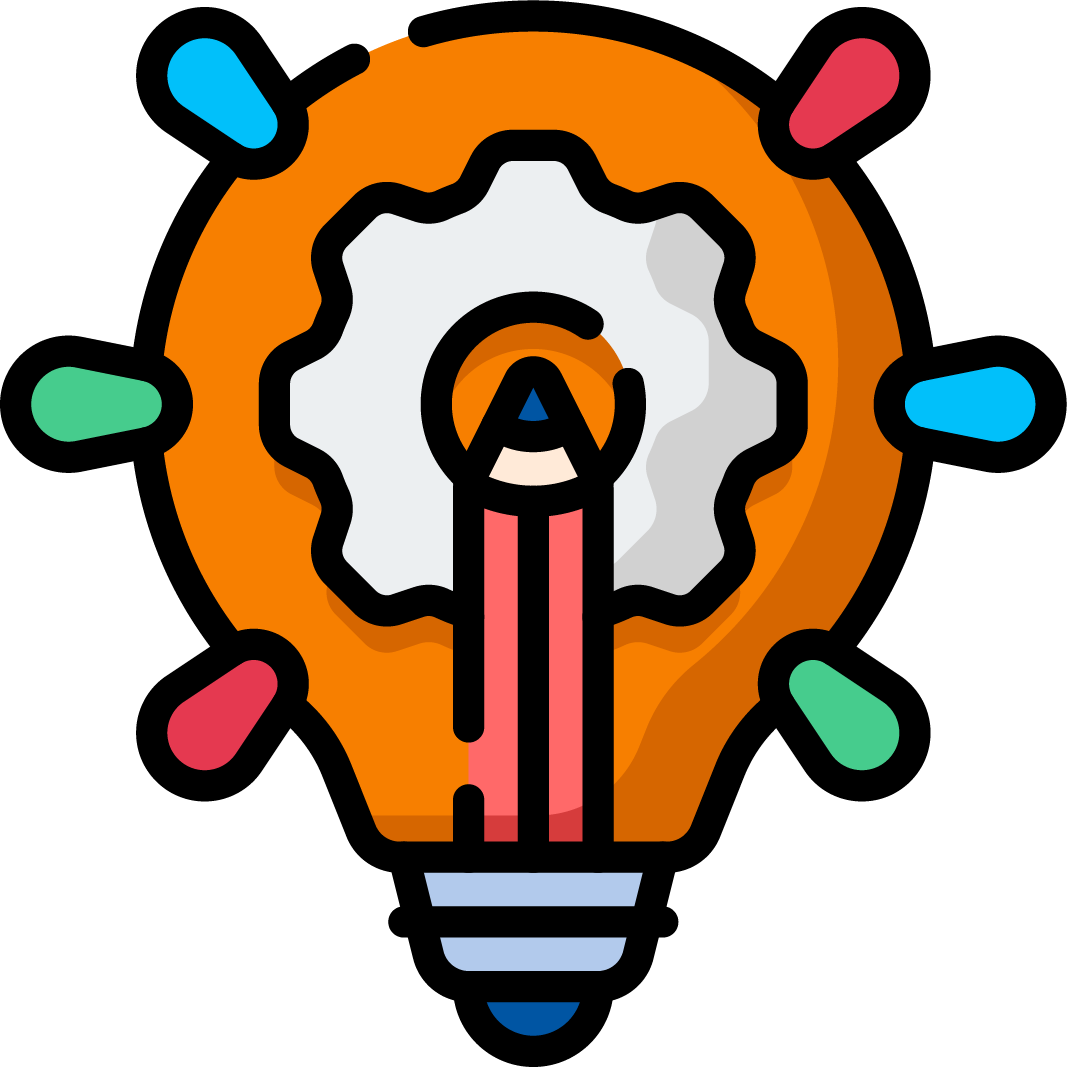
Free CAD Conversion
Our engineers will convert your drawings to digital format at no cost.
LET’S TALK BUSINESS
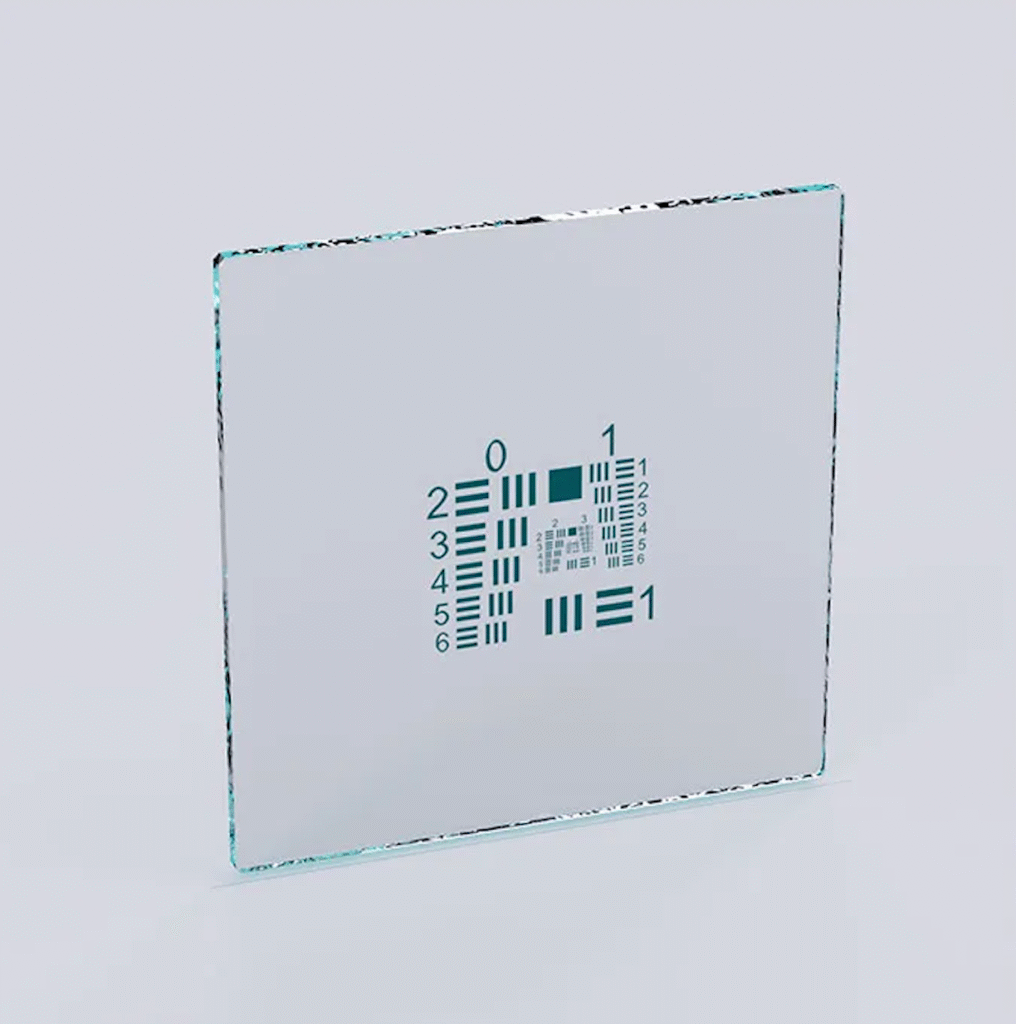
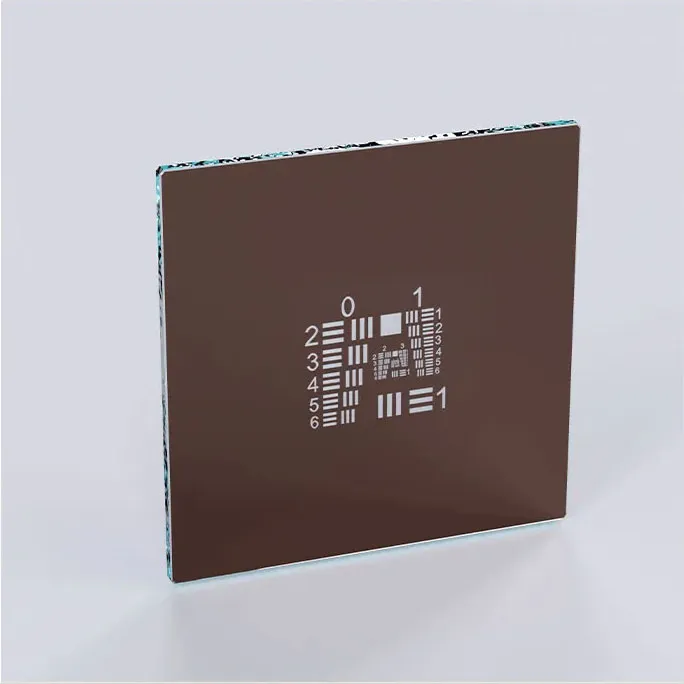
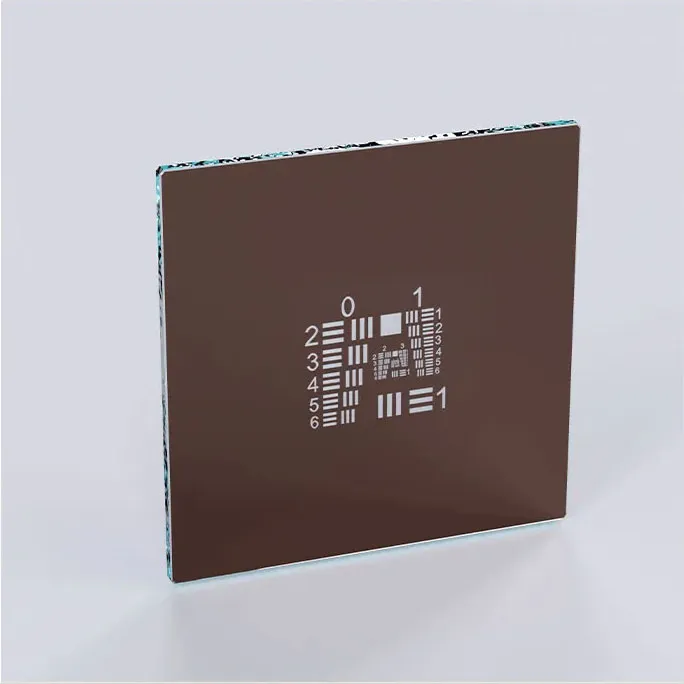
Tell us any of your requirements on test target:
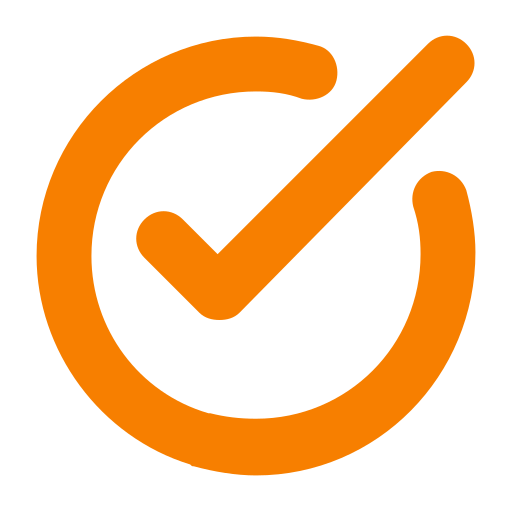
Custom Manufacturing (OEM/ODM)
– Purpose-built to your exact specs
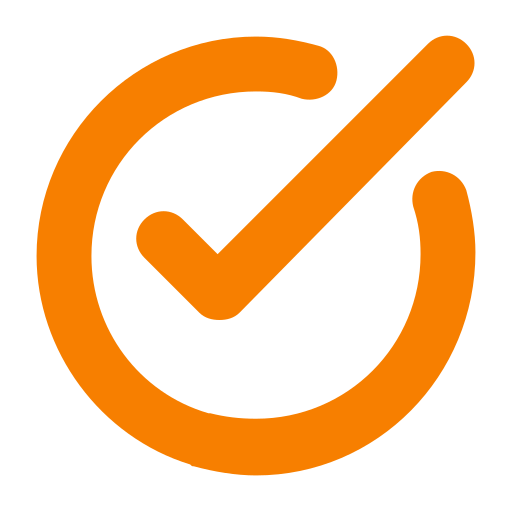
Low MOQ Starts from 1pcs
– End-to-end support from prototype to production
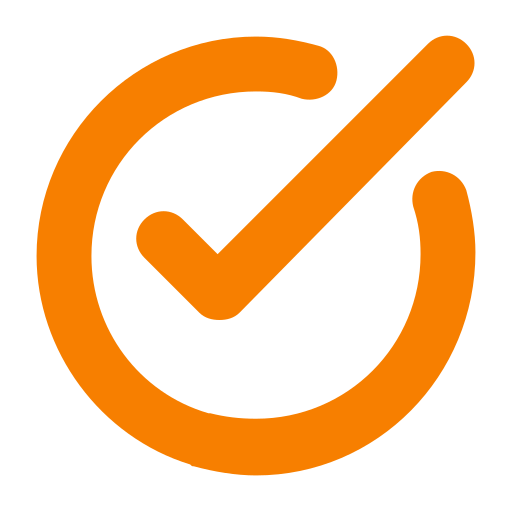
Trade & Distribution
– Volume discounts for channel partners
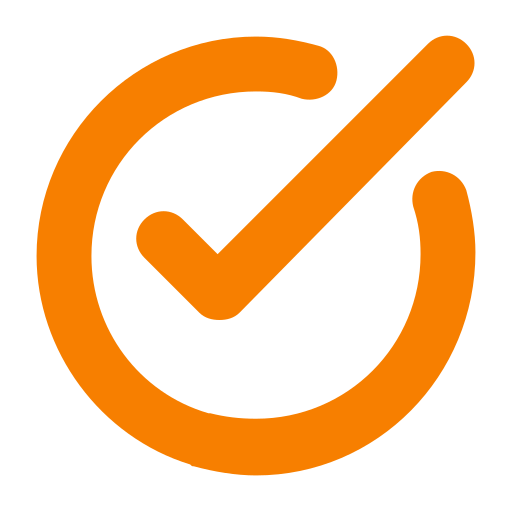
Global Sales & Support
– Build your brand with our proven quality
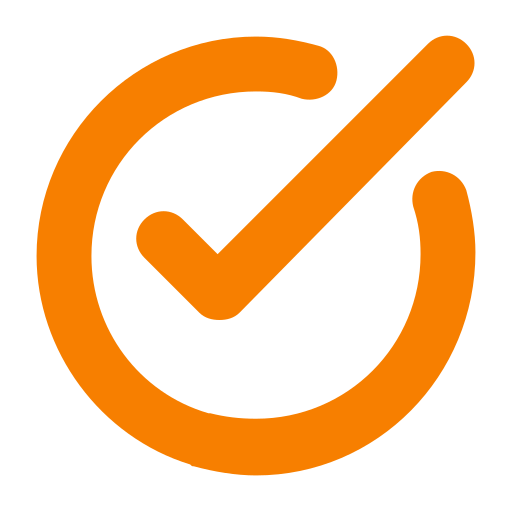
3rd-Party Certification
– Test our quality risk-free
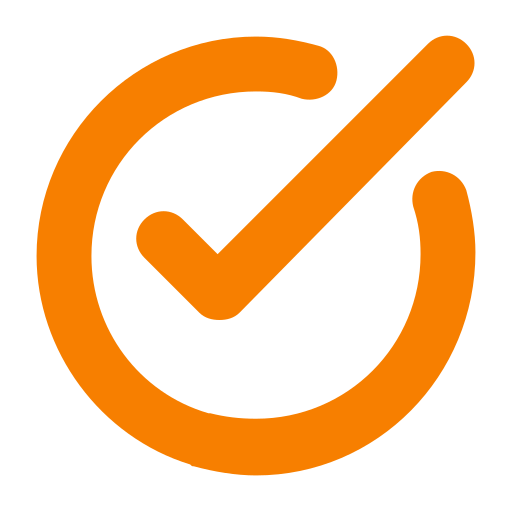
Fast-Track Quotes
– Competitive pricing delivered within 24 hours
Request A Quote
Please fill out our quote request form or email us at sales@calibvision.com, and we will get back to you within 24 hours!
FAQs
- Dimensional inspection reports
- Optical performance data
- Material certificates
- Traceability documentation