What is Calibration Target Accuracy?
There are two main ways we check if a calibration target is accurate enough. The first is called feature position accuracy, which is basically asking “Are all the dots or squares in exactly the right spots?” Think of it like this: imagine you drew a perfect grid on a piece of paper with a computer, then tried to print it out. Position accuracy tells you how close your printed version is to that perfect computer drawing. If some dots ended up a little too far left or right, or up or down, that would show up as poor position accuracy.
The second type is feature spacing accuracy, which asks a different question: “Are all the gaps between neighboring dots exactly the same size?” Picture a fence with evenly spaced posts. Even if each post is in roughly the right area, you’d still want the distance between post 1 and post 2 to be exactly the same as the distance between post 2 and post 3. That’s what spacing accuracy measures – the consistency of those gaps between features.
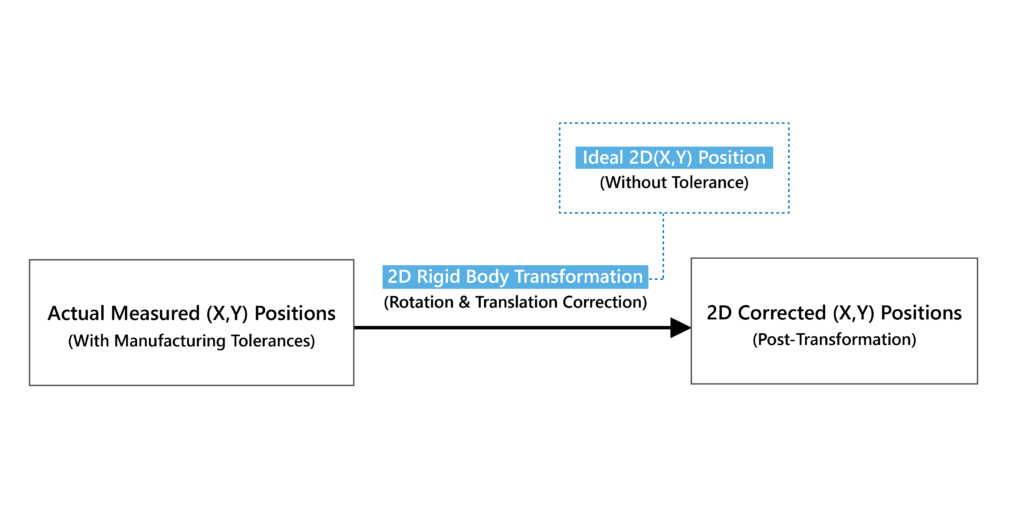
Figure 1: Position Deviation Analysis
9-Point Grid Pattern (3×3 Array)
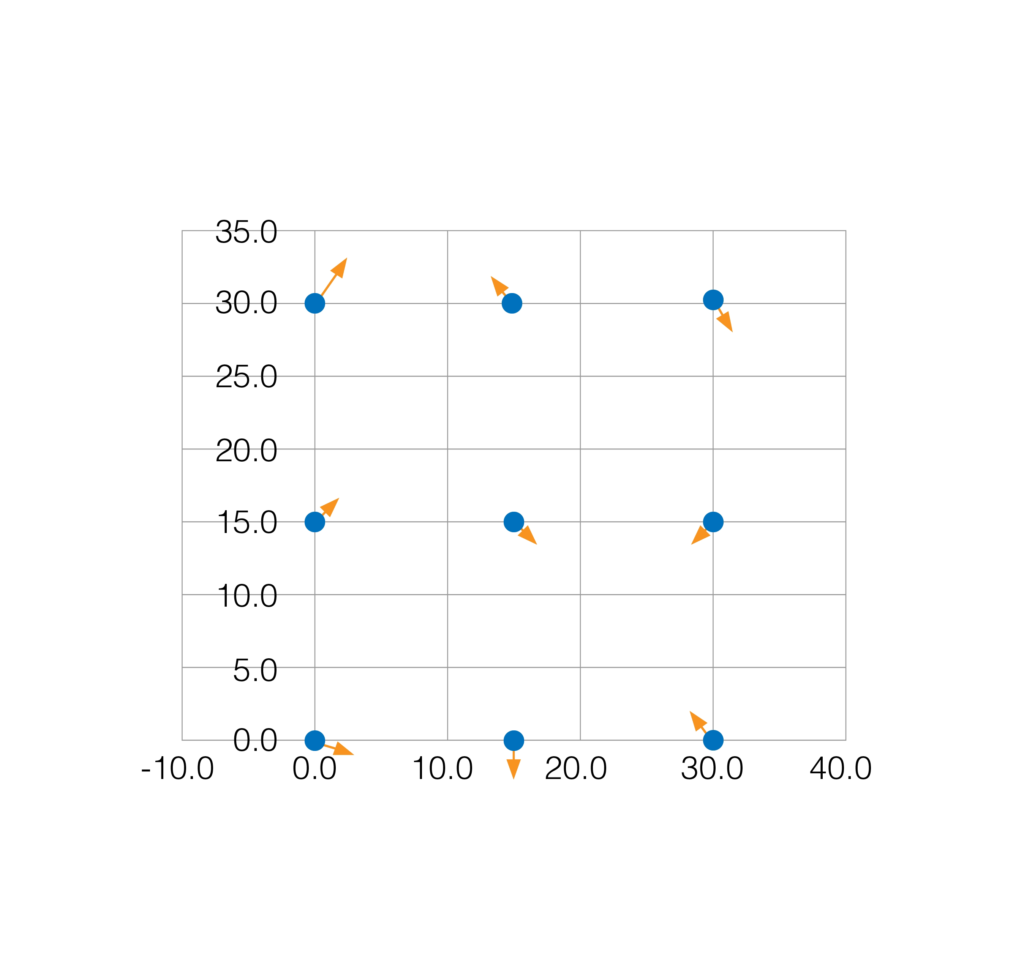
Figure 2: Pitch Accuracy Analysis
12 Adjacent Feature Pairs
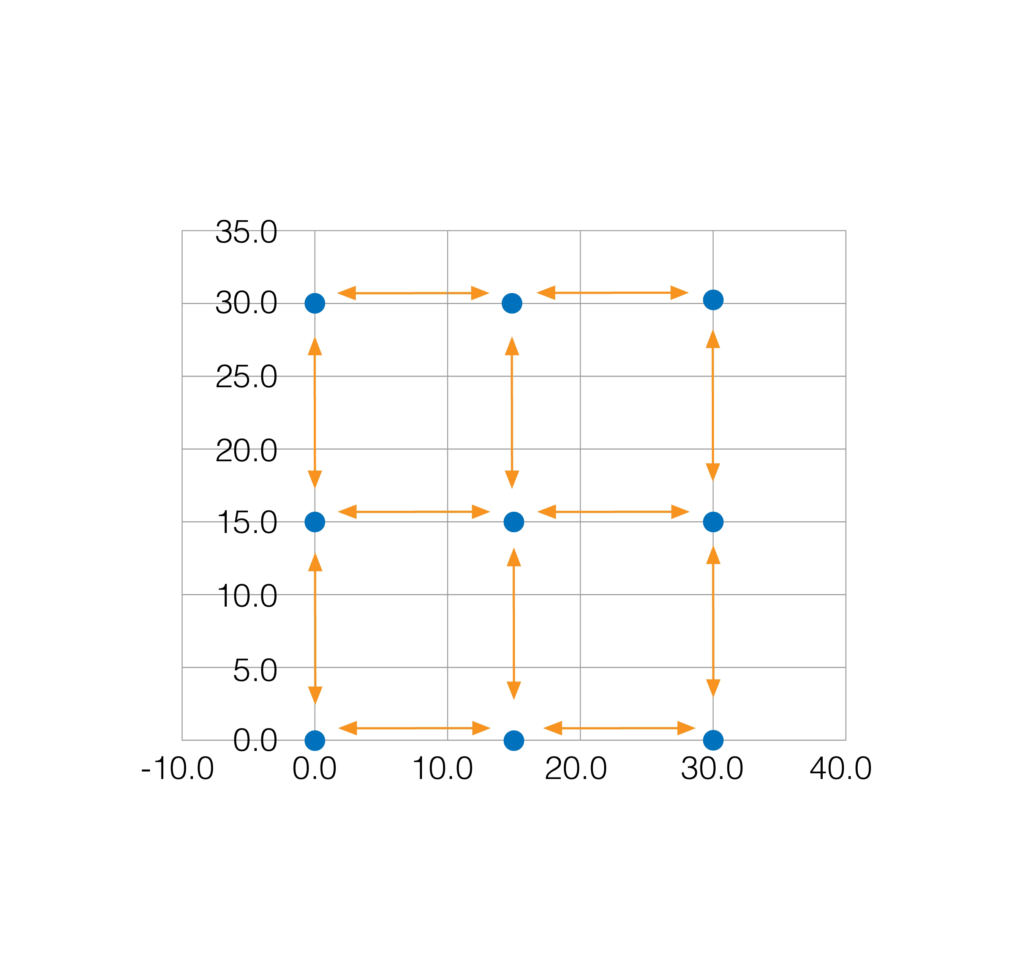
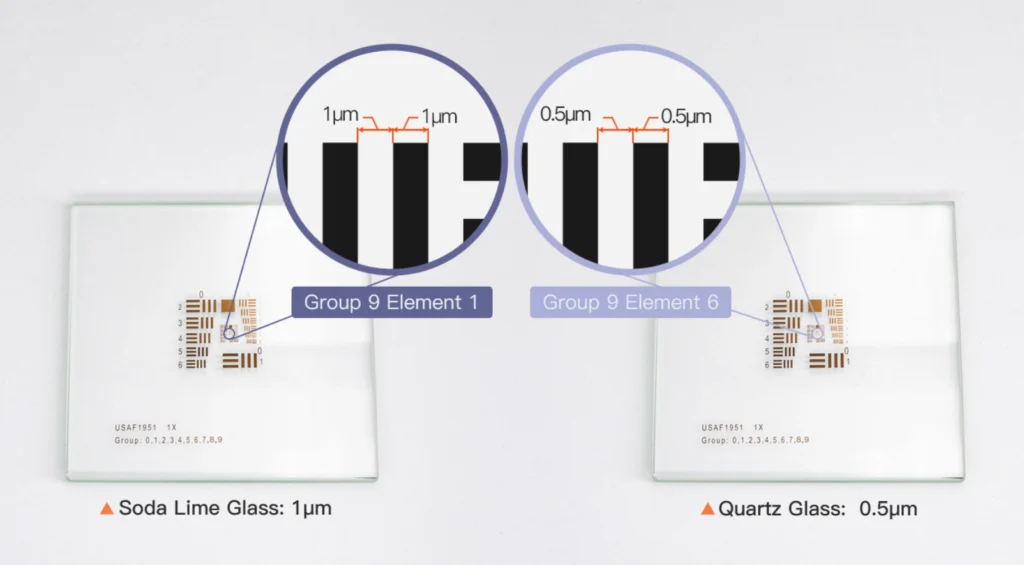
Measurement results and preparation
For most measurement results, the measured (x, y) positions may generally have an inclination or eccentricity effect regarding its ideal positions. The original (x, y) results are transformed by a best-fit 2D rigid transformation, which will not change relative position of all points, towards their ideal (x, y) value. After this transformation, the inclination and eccentricity effect of measured value can be eliminated.
Actual Measured (X, Y) positions | ||
---|---|---|
Point Index | Actual X/mm | Actual Y/mm |
1 | -0.00069 | 0.00028 |
2 | 14.99929 | 0.00006 |
3 | 30.00429 | 0.00048 |
4 | 0.00106 | 14.99828 |
5 | 15.00132 | 14.99835 |
6 | 30.00636 | 14.99805 |
7 | 0.00280 | 29.99889 |
8 | 15.00330 | 29.99928 |
9 | 30.00874 | 29.99897 |
Ideal 2D (X, Y) Position | ||
---|---|---|
Point Index | Target X/mm | Target Y/mm |
1 | 0 | 0 |
2 | 15 | 0 |
3 | 30 | 0 |
4 | 0 | 15 |
5 | 15 | 15 |
6 | 30 | 15 |
7 | 0 | 30 |
8 | 15 | 30 |
9 | 30 | 30 |
2D Affined (X, Y) Positions | ||
---|---|---|
Point Index | 2D Rigid Transformed X/mm | 2D Rigid Transformed Y/mm |
1 | -0.00264 | 0.00011 |
2 | 14.99734 | 0.00088 |
3 | 30.00234 | 0.00229 |
4 | -0.00188 | 14.99811 |
5 | 14.99838 | 14.99917 |
6 | 30.00342 | 14.99986 |
7 | -0.00113 | 29.99872 |
8 | 14.99937 | 30.00010 |
9 | 30.00481 | 30.00078 |
#01 Tolerance Analysis Example of
Feature Position Accuracy among Entire Pattern Area
For all 9 points, the positioning tolerance are calculated to know the tolerance distribution among the whole plate. And the maximum value of these tolerance will be Feature Position Accuracy among Entire Pattern Area. Here Point 9 (circled in red) has the maximum deviation from ideal positions, and the Feature Position Accuracy is 4.87μm.
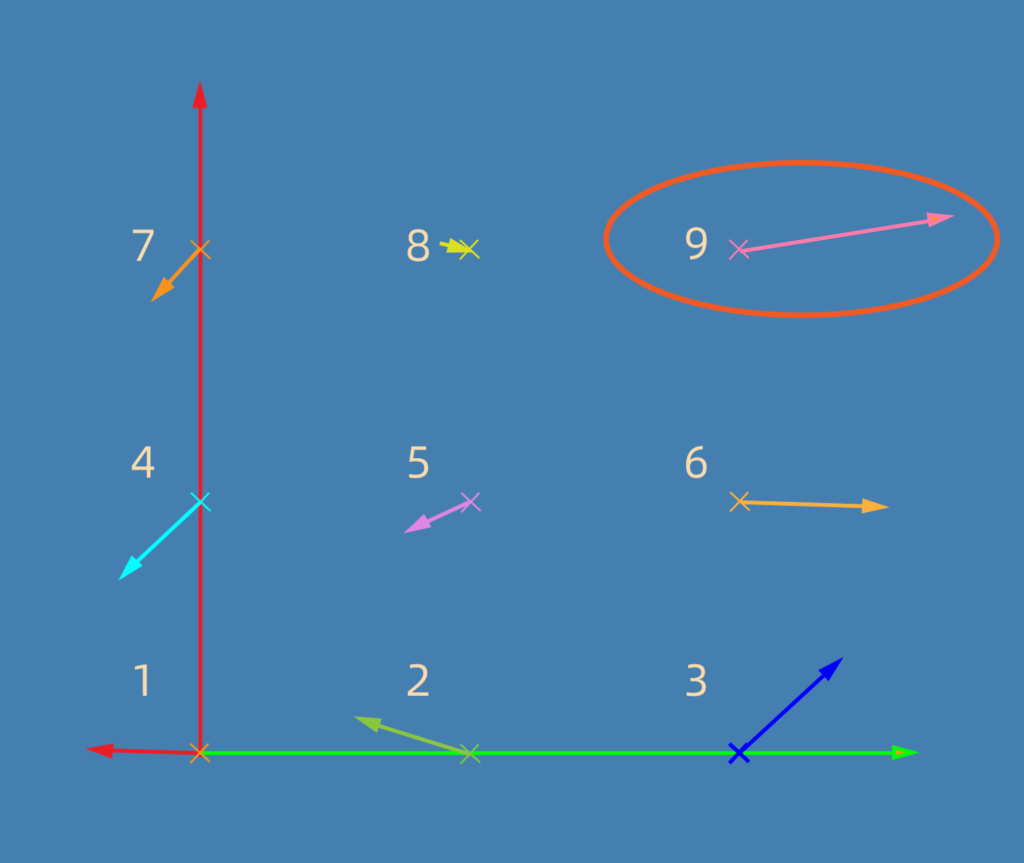
Feature Position Accuracy among Entire Pattern Area | |||
---|---|---|---|
Point Index | Tolerances X/mm | Tolerances Y/mm | Distance vector of a point to its ideal (x, y) location |
1 | -0.00264 | 0.00011 | 0.00264 |
2 | -0.00266 | 0.00088 | 0.00280 |
3 | 0.00234 | 0.00229 | 0.00327 |
4 | -0.00188 | -0.00189 | 0.00267 |
5 | -0.00162 | -0.00083 | 0.00182 |
6 | 0.00342 | -0.00014 | 0.00342 |
7 | -0.00113 | -0.00128 | 0.00171 |
8 | -0.00063 | 0.00010 | 0.00064 |
9 | 0.00481 | 0.00078 | 0.00487 |
#02 Tolerance Analysis Example of
Feature Spacing Accuracy of Any 2 Neighbor Points
There are totally 12 nearest-neighbor distances in 3 x 3 grid. Among these 12 distance values, the minimum and maximum value are -2.4um and +5.4um. It means, for the plate the Feature Spacing Accuracy of Any 2 Neighbor Points is [-2.4um, +5.4um].
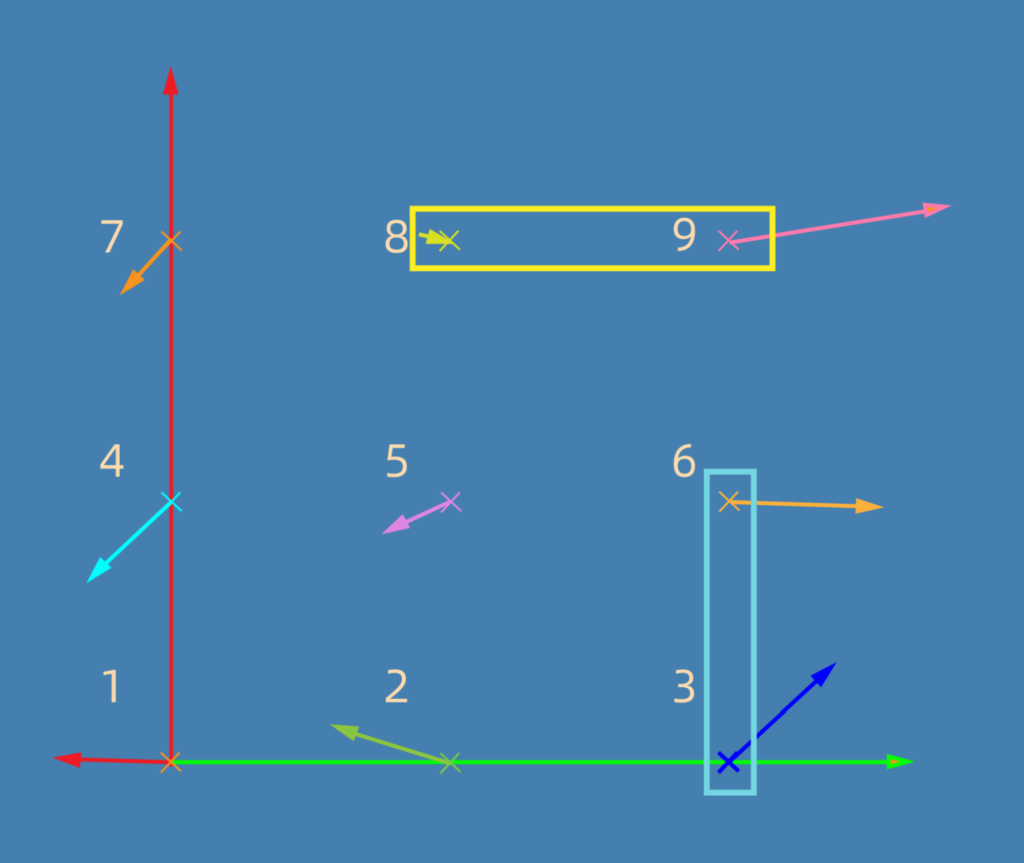
Feature Spacing Accuracy of Any 2 Neighbor Points (For 3 X 3 grid, there are 12 nearest-neighbor distances) |
||||
---|---|---|---|---|
Distance Index | Distance | Actual 2-Point Distance Values | Ideal 2-Point Distance Values | Tolerance (Actual - Ideal) |
1 | Distance(1,2) | 14.99998 | 15.00000 | 0.0000 |
2 | Distance(1,4) | 14.99800 | 15.00000 | -0.0020 |
3 | Distance(2,3) | 15.00500 | 15.00000 | 0.0050 |
4 | Distance(2,5) | 14.99829 | 15.00000 | -0.0017 |
5 | Distance(3,6) | 14.99757 | 15.00000 | -0.0024 |
6 | Distance(4,5) | 15.00026 | 15.00000 | 0.0003 |
7 | Distance(4,7) | 15.00061 | 15.00000 | 0.0006 |
8 | Distance(5,6) | 15.00504 | 15.00000 | 0.0050 |
9 | Distance(5,8) | 15.00093 | 15.00000 | 0.0009 |
10 | Distance(6,9) | 15.00092 | 15.00000 | 0.0009 |
11 | Distance(7,8) | 15.00050 | 15.00000 | 0.0005 |
12 | Distance(8,9) | 15.00544 | 15.00000 | 0.0054 |